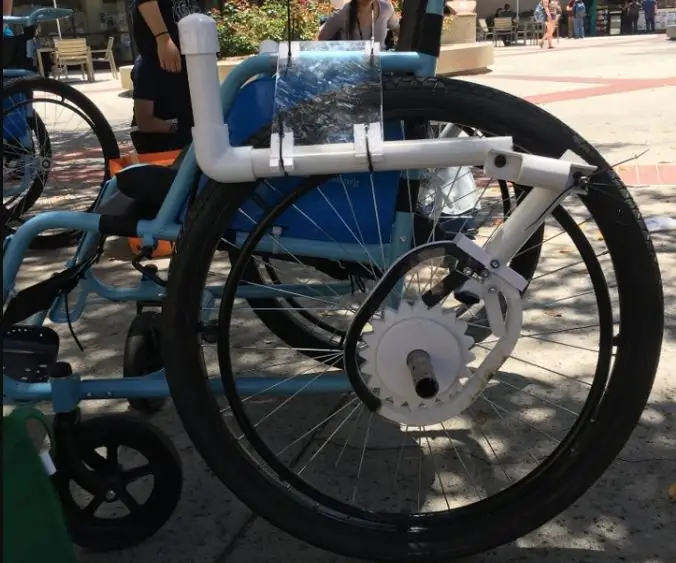
Оглавление:
- Шаг 1. Создайте внешнюю крышку корпуса для корпуса в SolidWorks
- Шаг 2: Создайте тело в SolidWorks
- Шаг 3: Создайте соединение в SolidWorks
- Шаг 4: Создайте рычаг / ручку в SolidWorks
- Шаг 5: Создайте подлокотник в SolidWorks
- Шаг 6: Создайте Gear в SolidWorks
- Шаг 7: Создайте собачку в SolidWorks
- Шаг 8: Создайте ручку направления в SolidWorks
- Шаг 9: Создайте крепление на трубе
- Шаг 10: Начало сборки в SolidWorks
- Шаг 11: заказ запасных частей у McMaster-Carr
- Шаг 12: приобретите детали в хозяйственном магазине
- Шаг 13: Изготовление деталей
- Шаг 14: Соберите все части вместе
- Шаг 15: Итеративное тестирование
- Шаг 16: Страница вкладов
2025 Автор: John Day | [email protected]. Последнее изменение: 2025-01-23 15:05
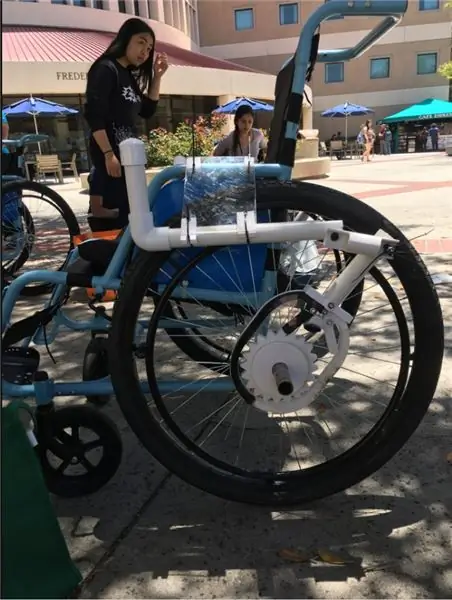
Обычная инвалидная коляска имеет много недостатков для людей со слабостью верхних конечностей или ограниченными ресурсами. Нашей команде было поручено разработать рычажный привод для инвалидных колясок из Миссии по освобождению инвалидных колясок, который позволил бы пользователям перемещаться дальше в своих креслах и помогал тем, у кого слабость верхних конечностей, использовать стулья. Привод рычага для инвалидной коляски Support System - это экономичное устройство, которое существенно снижает потребность в движении плеча и устраняет уровни усталости за счет использования горизонтальных рычажных приводов, а не вертикальных, которые подходят для ослабленных пациентов и пациентов в сельской местности. Типичный драйвер с вертикальным рычагом слишком сильно сосредотачивается на мышцах рук и плеч, что может вызвать осложнения у пациентов со слабостью верхних конечностей. Поэтому наша команда разработала горизонтальный рычажный привод, предназначенный для использования мышц груди, чтобы облегчить работу людям, которые не могут задействовать мышцы плеча.
Рыночное и ценностное предложение
Наш рычажный привод предназначен для решения проблемы боли и усталости в плече, которые связаны с использованием инвалидных колясок у людей, особенно из сельских деревень с немощеными дорогами, за счет использования движения вперед / назад, а не движения вверх / вниз вместе с улучшенный подлокотник для комфорта и поддержки. Поскольку сельские деревни и немощеные дороги обычно очень каменистые и неровные, пациенту придется приложить еще большее усилие к рычагу, чтобы переместить кресло-коляску на определенное расстояние по сравнению с гладкой дорогой. Таким образом, люди со слабостью верхних конечностей в сельской местности испытывают еще большие затруднения, потому что им требуется больше движения и силы, чтобы перемещаться с места на место, что вызывает проблемы, поскольку они постоянно становятся слабее, поскольку они продолжают использовать мышцы плеча изо дня в день.. Таким образом, с помощью горизонтального рычажного привода люди из сельской местности со слабыми верхними конечностями смогут не только свободно передвигаться, но и таким образом, чтобы уменьшить нагрузку на мышцы плеча, поскольку они вместо этого используют силу груди.
Анализ цен
Мы решили использовать ПВХ, акрил и АБС. Это был компромисс силы и стоимости. Эти три материала относительно дешевле, но достаточно прочные, чтобы работать должным образом. Ориентировочная стоимость - около 170 долларов. Изначально мы планировали использовать алюминий для большинства компонентов нашего рычажного привода, таких как внешний корпус и ручки рычага, потому что алюминий дешевле стали. Однако после проведения исследования мы увидели, что использование толстых листов и стержней алюминия не было бы идеальным решением из-за непомерно высоких затрат на получение значительного количества металла. Вместо этого мы нашли более дешевые альтернативы, используя разные материалы для разных деталей. Мы использовали большой акриловый лист для внешнего корпуса и разрезали его лазером на более мелкие части, что обошлось примерно в 25 долларов. Для сравнения, большие алюминиевые листы стоили бы более 70 долларов. Кроме того, мы также решили использовать трубы из ПВХ для наших ручек вместо металлических стержней, потому что трубы из ПВХ не только прочные, но и чрезвычайно дешевы. Хотя алюминиевые стержни могли быть более прочными, мы бы потратили около 30 долларов на каждую сторону инвалидной коляски. Напротив, трубы из ПВХ стоили около 5 долларов. Основная часть наших затрат приходится на 3D-печать из АБС-пластика. Поскольку мы напечатали три части нашей системы, общее время для печати всех этих частей заняло в общей сложности около 32 часов. В результате с почасовой оплатой использования 3D-принтера общая сумма составила 130 долларов.
Материалы и прототипирование дизайна
- труба ПВХ ~ 2,16 $
- Заглушка розетки ПВХ ~ 1,66 $
- ПВХ отвод под углом 90 градусов ~ 2,28 $
- Акриловый лист ~ 24,98 $
- Шестерни АБС, собачки АБС, ручки АБС ~ 130 $
- Стальные винты ~ 6,92 $
- Резинки ~ 3,18 $
- Клей для рукоделия E6000 ~ 4,29 $
Шаг 1. Создайте внешнюю крышку корпуса для корпуса в SolidWorks
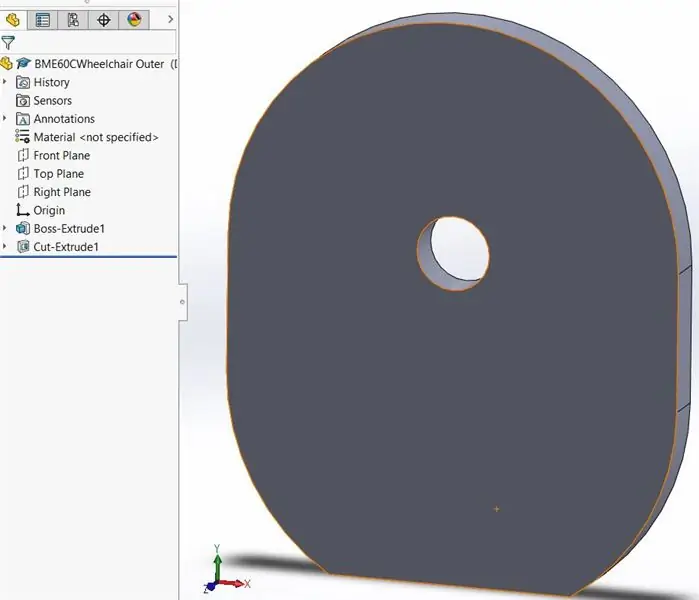
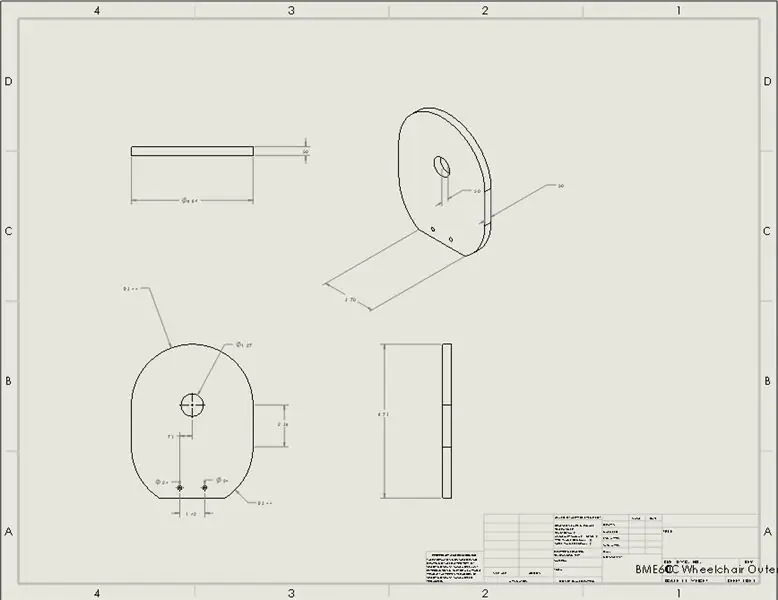
Перед запуском всего проекта установите размеры с помощью MMGS.
Используя переднюю плоскость, создайте новый эскиз и нарисуйте круг в исходной точке диаметром 175 мм. Затем нарисуйте две вертикальные линии с касательными к окружности, каждая из которых составляет 60 мм. После нарисуйте касательные дуги на концах обеих линий и соедините их горизонтальной линией. Затем, используя функцию «обрезать объекты», обрежьте нижнюю половину круга внутри области.
Как только эскиз будет завершен, бобышка выдавите эскиз, используя слепое выдавливание на 12,70 мм. Как только выдавливание будет завершено, откройте новый эскиз и нарисуйте круг, совпадающий с вершиной касательных линий диаметром 32,20 мм, и вырежьте выдавливание, используя «сквозное отверстие», сделайте отверстие.
Чтобы сделать два нижних круга, откройте новый эскиз и нарисуйте два круга диаметром 6 мм, расположив их на расстоянии 15 мм от дна и 58,84 мм от центра касательной дуги. Когда эскиз будет завершен, используйте выдавливание, используя «через все», чтобы сделать два отверстия.
Шаг 2: Создайте тело в SolidWorks
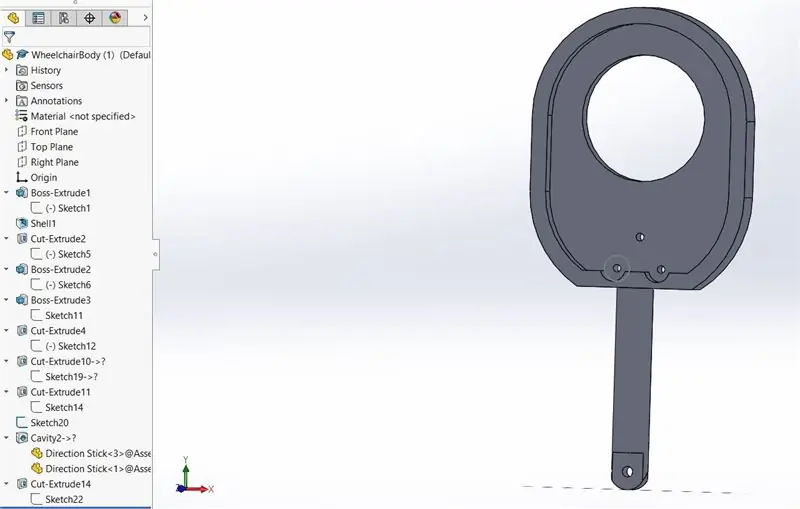
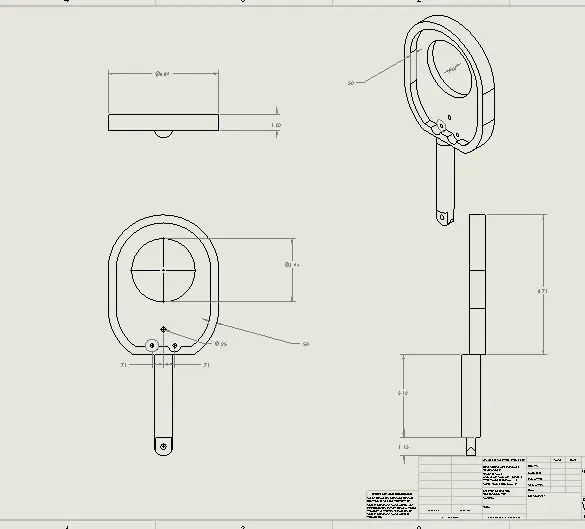
Чтобы начать тело, повторите эскиз, как в первой части, чтобы создать общую форму тела и выдавить ее на 25,40 мм. После выдавливания детали используйте опцию оболочки на одной из граней детали размером 12,70 мм.
После этого откройте новый эскиз и нарисуйте круг в центре детали диаметром 100 мм, который находится на расстоянии 133,84 мм от низа и 87,50 мм от боковых сторон детали. Как только эскиз будет завершен, вырежьте выдавливание, снова используя «через все», чтобы создать отверстие.
Чтобы создать рычаг, создайте новый эскиз на верхней плоскости и поверните деталь вниз. Начните набросок с создания круга диаметром 28,74 мм в основании предыдущей части и выдавите его на 130 мм.
После создания рычага создайте новый эскиз у основания рычага. Нарисуйте две горизонтальные линии, равноудаленные от начала координат, длиной 25,10 мм. После этого соедините две линии касательными дугами высотой 14 мм. Как только эскиз будет завершен, выдавите новый эскиз вслепую на 30 мм.
Используя новейшую выдавленную деталь, создайте новый эскиз на передней плоскости и нарисуйте круг на расстоянии 14,95 мм от вершины и 12,55 мм от стороны. Затем разрежьте экструдированный материал насквозь, чтобы получилось отверстие.
Для всего корпуса нарисуйте два отверстия в нижней части корпуса диаметром 6 мм на расстоянии 36 мм друг от друга, 15 мм от низа и 58,84 мм от верха касательных дуг. После этого прорежьте экструдер через все, чтобы сделать два отверстия.
Внизу детали создайте новый эскиз. Проведите прямые линии с обеих сторон 14,93 мм. Проведите горизонтальную линию шириной 28,74 мм, чтобы соединить две линии. Нарисуйте круг с радиусом 14,37 мм и совместите его с кругом в центре. Обрежьте его, чтобы получился полукруг. Вырежьте экструзию через всю фигуру в форме пандуса в нижней части детали, чтобы оставить закругленный край.
* Чтобы подготовиться к полости, создайте новый эскиз на задней плоскости. Нарисуйте круг радиусом 20,57 мм на расстоянии 15 мм от низа и 58,84 мм от боковой касательной дуги. После сборки всех частей вместе вы редактируете деталь в сборке и используете полость для создания полукругов.
На лицевой плоскости сделайте новый набросок. Нарисуйте круг в центре диаметром 6,35 мм между большим кругом и двумя маленькими кругами внизу. Сделайте окружность на расстоянии 40,13 мм от дна и 33,70 мм от касательной дуги по бокам. После этого прорежьте все, чтобы создать небольшой круг в центре.
* Этот шаг будет продолжен позже, после сборки всех частей вместе.
Шаг 3: Создайте соединение в SolidWorks
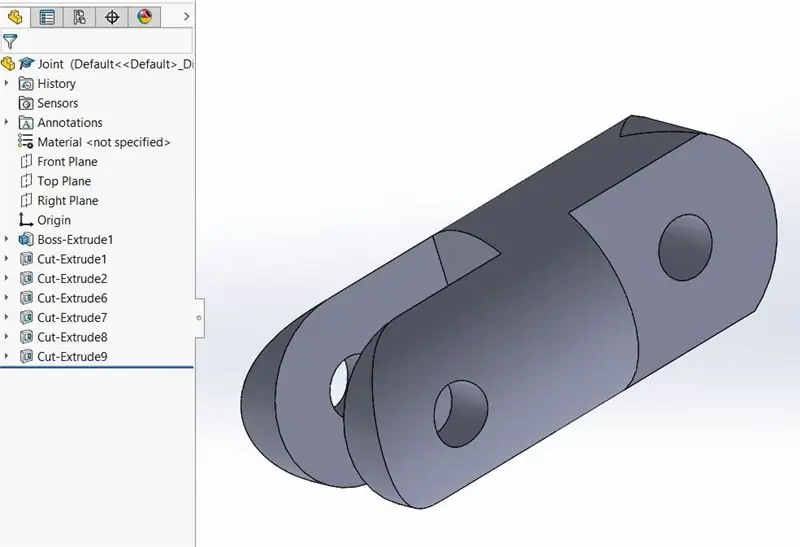
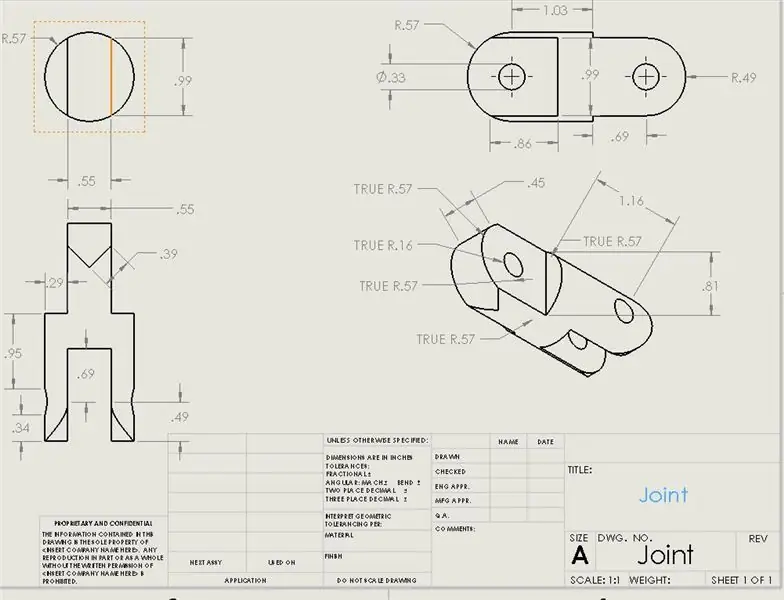
Чтобы начать соединение, начните с создания нового эскиза на передней пластине и нарисуйте круг диаметром 28,74 мм. Слепым выдавите только что нарисованный круг на 120 мм.
Затем поверните деталь и нарисуйте на обратной стороне. Нарисуйте две вертикальные линии длиной 25,10 мм и 7,37 мм от края круга. и вырезать экструдер с использованием «слепых» и глубиной 30 мм для обеих областей.
Затем, глядя с правой плоскости, нарисуйте круг в области, которую мы только что вырезали. Диаметр должен быть 8,38 мм с расстоянием 12,55 мм от верхнего края и 14,95 мм от бокового края. Сделайте глухой пропил 30 мм.
На правой плоскости с обеих сторон проведите прямые линии шириной 15,05 мм. Проведите вертикальную линию длиной 28,74 мм, чтобы соединить две линии. Нарисуйте круг радиусом 14,37 мм и совместите его с кругом в центре. Обрежьте его, чтобы получился полукруг. Вырежьте экструзию через всю фигуру в форме пандуса в нижней части детали, чтобы края остались закругленными.
После этого, если смотреть с задней панели, нарисуйте две вертикальные линии длиной 25,10 мм и 7 мм от центра. Сделайте глухой пропил глубиной 35 мм.
На правой плоскости нарисуйте круг в правой части с центром на расстоянии 17,24 мм от левого края детали.
На правой плоскости повторите фигуру в форме пандуса на левой стороне детали.
Шаг 4: Создайте рычаг / ручку в SolidWorks
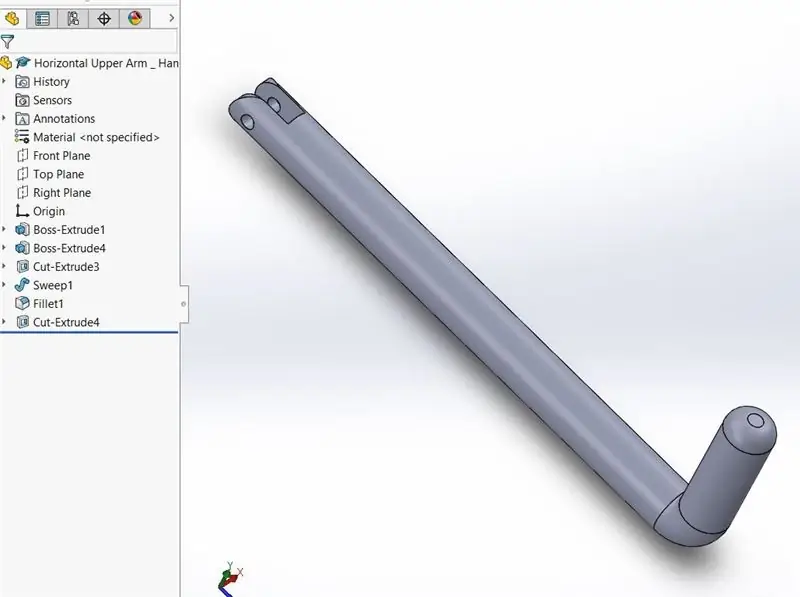
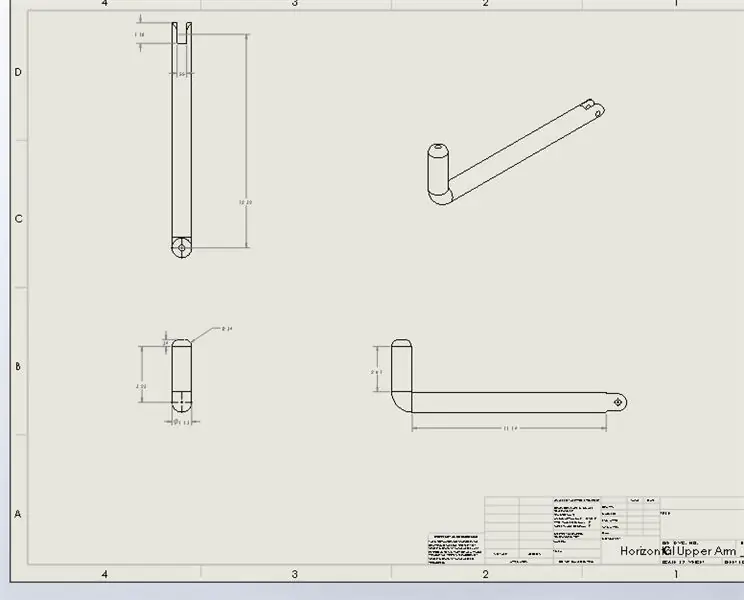
На передней плоскости нарисуйте круг диаметром 28,75 мм в начале координат. Бобышка выдавили его на 275 мм.
Затем перейдите к задней плоскости и нарисуйте две вертикальные линии длиной 25,10 мм на расстоянии 7 мм от центра. Выдавите две линии так, чтобы в середине образовался зазор с размером выдавливания 35 мм.
На детали, которую мы только что выдавили, нарисуйте круг диаметром 8,40 мм с расстоянием 17,76 мм от центра круга до края и 12,56 мм от низа детали. Вырежьте экструдер насквозь, чтобы образовалось отверстие.
На правой плоскости создайте короткую линию длиной 9,24 мм, которая соединяется с самой левой частью детали. Нарисуйте дугу радиусом 30 мм. Затем нарисуйте вертикальную линию, соединяющую другой конец дуги длиной 76,39 мм. После завершения эскиза разверните эскиз.
После этого скруглите верхнюю часть детали, которую мы только что подняли, на 10 мм.
Наконец, в правой плоскости нарисуйте прямые горизонтальные линии с обеих сторон детали с созданным нами отверстием длиной 17,78 мм. Проведите вертикальную линию длиной 25,10 мм, чтобы соединить две линии. Нарисуйте круг радиусом 12,56 мм и совместите его с кругом в центре. Обрежьте его, чтобы получился полукруг. Вырежьте экструзию через всю фигуру в форме пандуса в нижней части детали, чтобы оставить закругленный край.
Шаг 5: Создайте подлокотник в SolidWorks
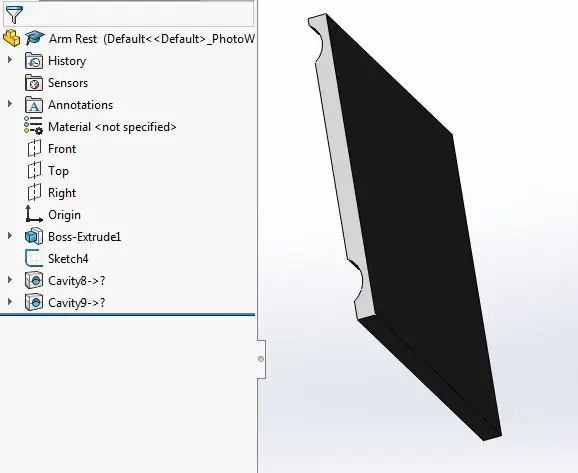
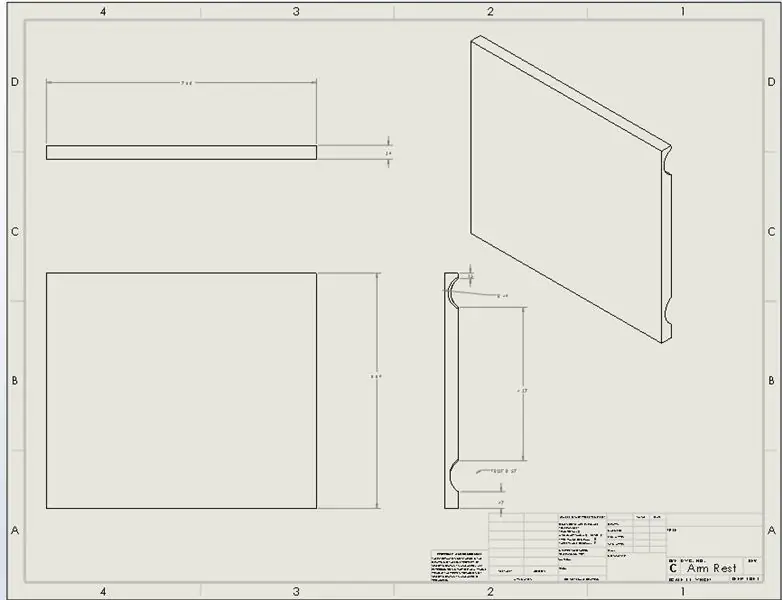
На передней плоскости нарисуйте прямоугольник высотой 170 мм и длиной 195 мм и сделайте слепой профиль 10 мм.
* После сборки используйте полость, чтобы создать углубления на прямоугольной призме.
Шаг 6: Создайте Gear в SolidWorks
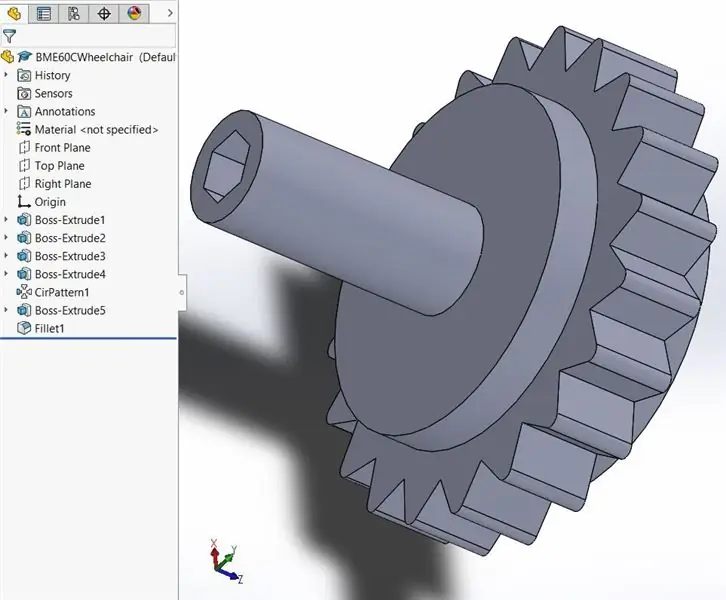
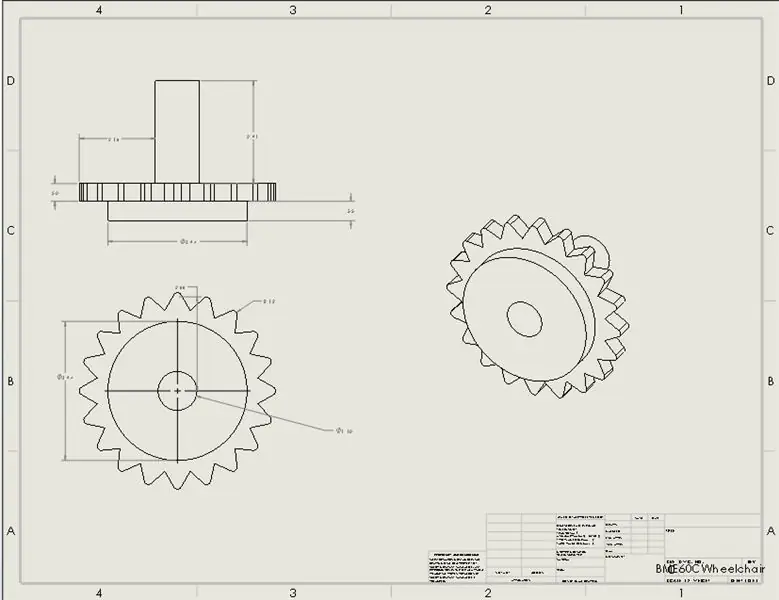
Чтобы начать передачу, создайте новый эскиз на передней плоскости и нарисуйте два круга из той же точки с диаметрами 25,40 мм и 31,75 мм. Затем выдавите бобышку слепым выдавливанием на 30 мм.
После завершения экструзии создайте еще один эскиз на передней плоскости и нарисуйте еще один круг диаметром 31,75 мм и выдавите 20 мм.
Затем нарисуйте на передней плоскости круг диаметром 100 мм и выдавите его на 12,70 мм.
В верхней части только что выдавленной детали нарисуйте равносторонний треугольник со сторонами 30 мм. Выдавите треугольник 12,70 мм.
После завершения экструзии используйте функцию кругового массива, чтобы вокруг детали было 20 однородных треугольников. Затем скруглите все края треугольников.
На передней плоскости нарисуйте еще один круг диаметром 100 мм и выдавите его на 13,97 мм.
Чтобы создать отверстие в середине шестерни, нарисуйте круг на задней плоскости диаметром 27,94 мм и вырежьте экструдер до поверхности.
Шаг 7: Создайте собачку в SolidWorks
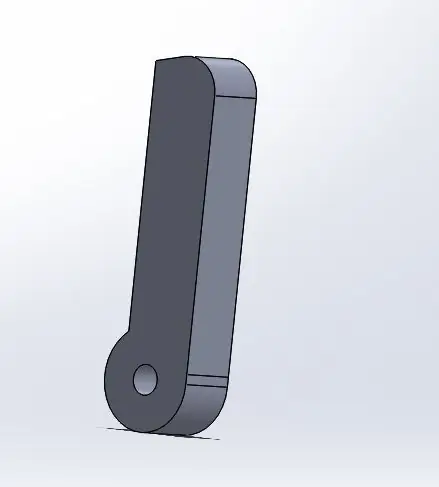
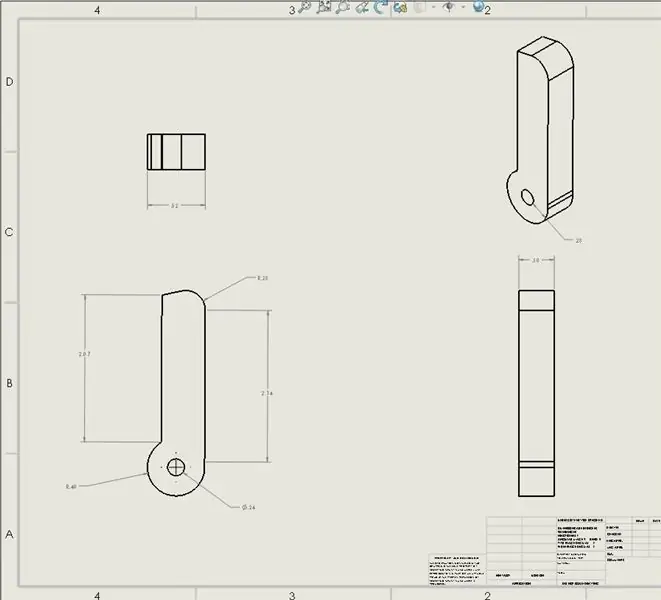
На лицевой плоскости проведите вертикальную линию длиной 2,07 дюйма. После этого нарисуйте дугу радиусом 0,40 дюйма, соединяющуюся с нижней частью вертикальной линии. Также нарисуйте горизонтальную линию, соединенную с верхним краем вертикальной линии. Используя интеллектуальные размеры, щелкните верхний край, а затем вертикальную линию и установите угол 78,00 градусов.
После того, как угол установлен, нарисуйте еще одну вертикальную линию, которая соединяется с наклонной линией длиной 2,14 дюйма. Затем скруглите край этой линии с горизонтальной линией с радиусом 0,28 дюйма.
Как только эскиз будет завершен, выдавите бобышку с помощью слепого выдавливания 0,5 дюйма. Чтобы создать отверстие в середине, нарисуйте круг с радиусом 0,12 дюйма в центре детали и используйте вырез и выдавливание через все.
Шаг 8: Создайте ручку направления в SolidWorks
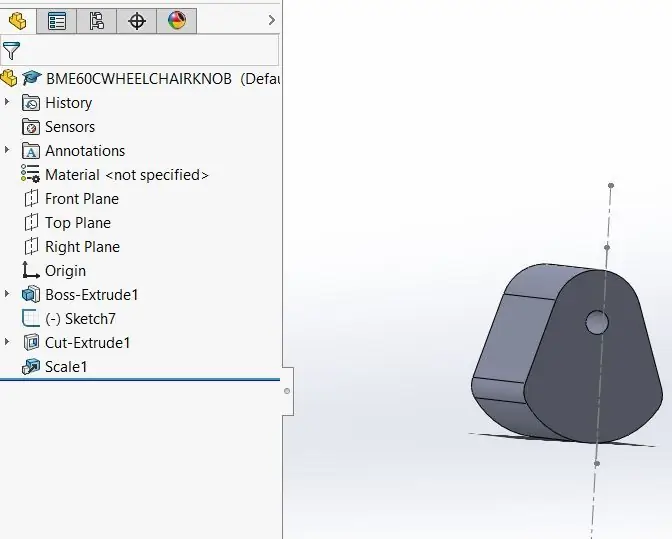
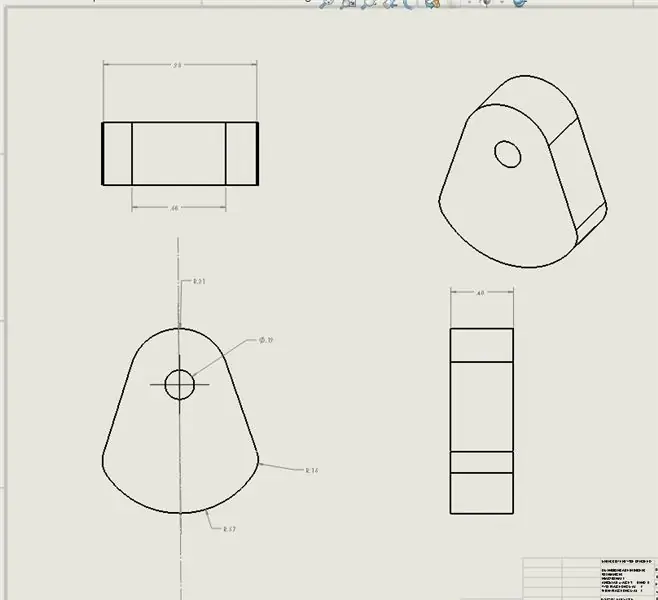
На передней плоскости нарисуйте вертикальную центральную линию. Затем наверху центральной линии нарисуйте дугу радиусом 10 мм. Затем с обеих сторон нарисуйте наклонные линии длиной 18,26 мм. Затем нарисуйте дугу с обеих сторон радиусом 5 мм. Чтобы соединить обе стороны, нарисуйте еще одну дугу радиусом 18 мм. Выдавите эскиз, используя слепое выдавливание 12,70 мм.
Чтобы создать отверстие, нарисуйте круг диаметром 5,90 мм, центр которого находится на расстоянии 8 мм от начала координат. Используйте выдавливание до поверхности.
Масштабируйте деталь относительно центра тяжести с масштабным коэффициентом 0,8 мм.
Шаг 9: Создайте крепление на трубе
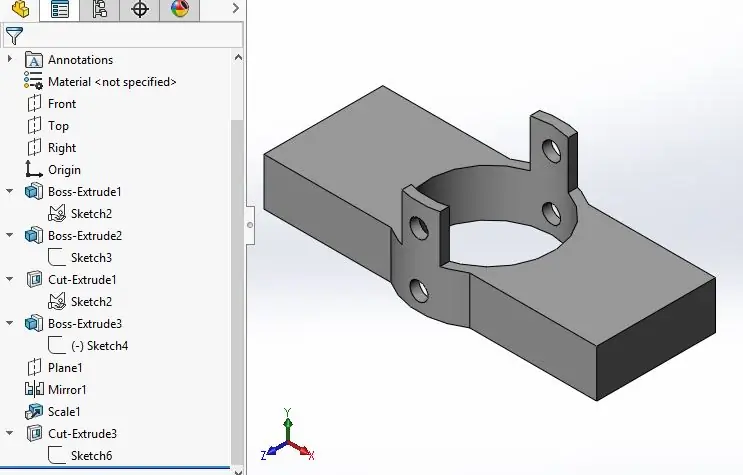
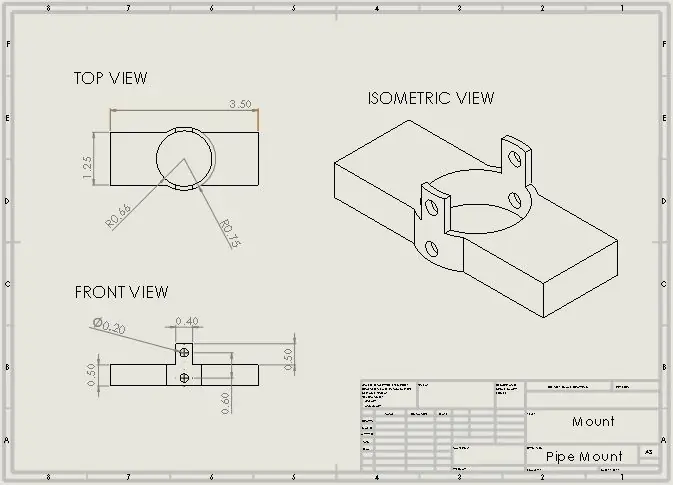
Чтобы создать крепление для трубы, которое будет прикреплять плечо рычага к корпусу шестерни, начните с эскиза двух окружностей. Внутренний круг должен иметь диаметр трубы из ПВХ, чтобы он мог легко скользить по нему, поэтому он должен быть 1,3125 дюйма. Внешний круг должен быть около 1,5 дюймов. Убедитесь, что два круга концентрически, и выдавите часть между двумя кругами на 0,5 дюйма. Затем нарисуйте прямоугольник, соответствующий нижней поверхности внешнего кожуха шестерни. Это будет прямоугольник размером 3,5 на 1,25 дюйма. Центрируйте этот прямоугольник вокруг круга, установив длинный край прямоугольника на расстоянии 1,75 дюйма от центра круга, а короткий край прямоугольника - на 0,63 дюйма от центра круга. Выдавите прямоугольник на 0,5 дюйма. Поскольку некоторые части прямоугольника лежат внутри внутреннего круга, вырезать выдавить внутренний круг, чтобы очистить его. Затем от верхней плоскости детали нарисуйте центральную линию от круга до внешней части выдавленного края. Из этой центральной точки на выдавленном крае нарисуйте прямоугольник, идущий на 0,2 дюйма в обе стороны. Выдавите этот маленький прямоугольник на 0,5 дюйма. Создайте опорную плоскость передней поверхности через центр детали и используйте функцию зеркального отражения, чтобы создать идентичный выдавленный прямоугольник на другой стороне круга.
При 3D-печати деталей всегда рекомендуется немного увеличивать масштаб, чтобы избежать помех при размещении детали на сборке. В этом случае масштаб всей части был увеличен на 1,05. Наконец, нарисуйте два круга диаметром 1/4 дюйма, расположенные на лицевой стороне центра детали: один на маленьком прямоугольнике, а другой на стороне круга. Убедившись, что два круга связаны друг с другом по вертикали, их можно разрезать через всю деталь, вырезав всего четыре круга. Это будут отверстия, в которые можно вставить болты для соединения ПВХ с основным корпусом корпуса редуктора.
Шаг 10: Начало сборки в SolidWorks
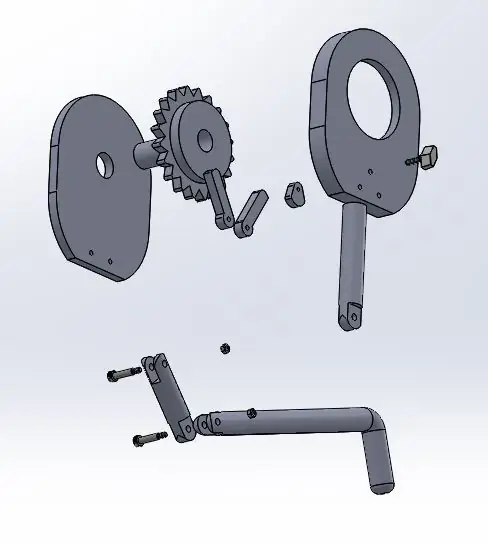
Сначала вставьте все детали, созданные в предыдущих шагах, вместе с имеющейся в наличии внешней ручкой, винтами и гайками, сделав корпус кресла-коляски основным компонентом.
Начните с соединения корпуса и шестерни, щелкнув по краю шестерни и краю корпуса, и используйте концентрическое сопряжение. Затем щелкните грань шестерни и тело, чтобы создать совпадающую деталь.
Затем соедините тело и ручку направления, щелкнув грань ручки направления и тело, чтобы создать совпадающее сопряжение.
Теперь соедините внешнюю ручку и корпус кресла-коляски, щелкнув по поверхности внешней ручки и по корпусу, чтобы создать совпадающую пару.
Создайте концентрическое сопряжение, щелкнув грань тела и грань внешней ручки.
Затем сделайте концентрическое сопряжение, щелкнув лицевую сторону ручки направления и край тела.
Теперь щелкните грани тела и собачки, чтобы создать совпадающее сопряжение, и повторите для другой собачки.
Создайте касательное сопряжение, щелкнув по поверхности ручки направления и защелки, и повторите для другой защелки.
Затем создайте совпадающее сопряжение, щелкнув грань тела и внешний кожух, и сделайте концентрическое сопряжение, щелкнув грань тела и край внешнего кожуха. Затем сделайте лицевую часть тела параллельной лицевой стороне внешнего футляра.
Создайте предельный угол, который имеет максимальное значение 78 градусов и минимальное значение 35 градусов для лицевой стороны тела и лицевой стороны собачки, и повторите для другой собачки.
Затем соедините соединение и тело, щелкнув по граням обоих, чтобы создать концентрическое сопряжение. Затем создайте сопряжение по центру по ширине для обеих граней соединения и тела.
Затем создайте концентрическое сопряжение для края плеча рычага и края соединения. Создайте еще одно сопряжение по центру по ширине для обеих сторон шарнира и плеча рычага.
Сделайте еще одно концентрическое сопряжение для поверхности соединения и винта. Затем создайте касательное сопряжение, щелкнув грань соединения и грань винта.
На правой плоскости нарисуйте две осевые линии для будущего сопряжения, при этом первая линия проходит там, где тело встречается с суставом, а вторая - где сустав встречается с плечом рычага.
Затем создайте концентрическое сопряжение, щелкнув поверхность плеча рычага и второй винт. После совмещения создайте еще одно касательное сопряжение с гранями обоих компонентов.
Нарисовав ранее первую ось, совместите кромку первой гайки и ось, чтобы создать концентрическое сопряжение.
Используйте совпадающее сопряжение для поверхности первого винта и первой гайки и повторите действия для второго винта и гайки.
Сделайте концентрическое сопряжение кромкой второй гайки и второй оси.
Создайте еще одно концентрическое сопряжение с лицевой стороной корпуса и внешней гранью первого винта. Вдобавок сделайте совпадающую пару для этих частей.
Сделайте концентрическое сопряжение для торца собачки и внешней грани третьего винта.
Создайте совпадающее сопряжение с гранью корпуса и внешней гранью третьего винта.
Затем создайте еще одно концентрическое сопряжение, щелкнув поверхность внешнего корпуса и внешнюю поверхность третьего винта и совместив их.
Сделайте концентрическое сопряжение, щелкнув поверхность тела и поверхность собачки и совместив их. Повторите то же самое для другой собачки.
Сделайте концентрическое сопряжение, щелкнув по поверхности ручки направления и внешней ручки.
Наконец, совместите грань тела и край ручки направления, чтобы создать концентрическое сопряжение.
Шаг 11: заказ запасных частей у McMaster-Carr
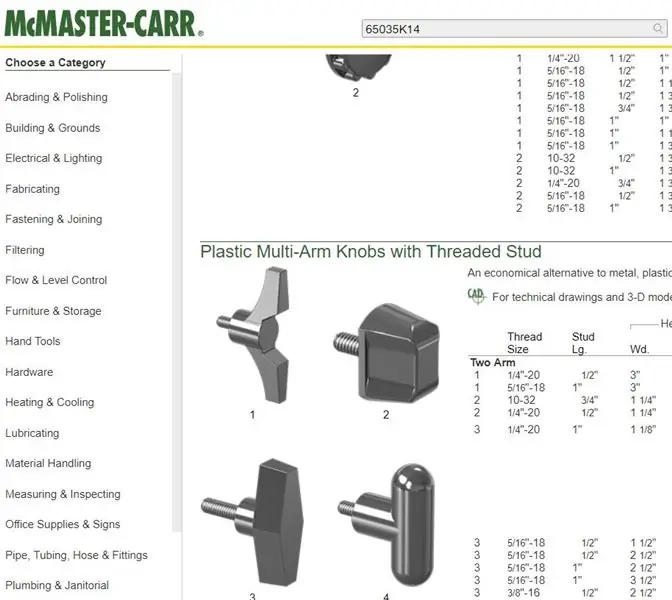
Закажите пластиковую ручку с двумя рычагами (внешняя ручка), винт с буртиком из легированной стали, стальные шестигранные гайки и кабельные стяжки у McMaster-Carr. Номера позиций: 65035K14, 92981A205, 90592A016 и 70215K61 соответственно.
Шаг 12: приобретите детали в хозяйственном магазине
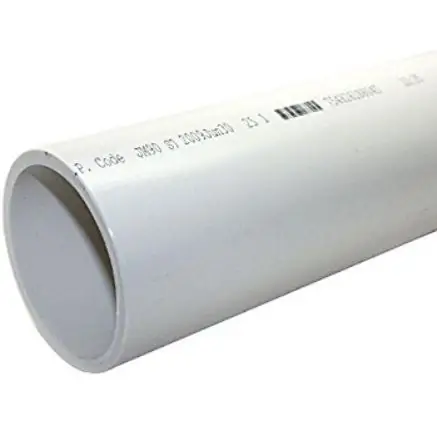
В местном хозяйственном магазине приобретите следующее:
- акриловый лист 18 дюймов x 24 дюйма x 0,220 дюйма
- Прозрачный клей (клей E6000)
- Заглушка для гнезда из ПВХ 1 дюйм (2)
- ПВХ труба с гладким концом 1 дюйм x 10 футов
- 1-дюймовый отвод 90 градусов из ПВХ (2)
Шаг 13: Изготовление деталей
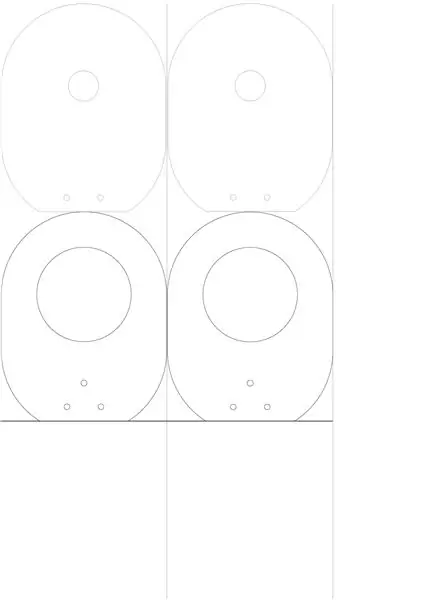
Детали, напечатанные на 3D-принтере: подготовьте детали SolidWorks и преобразуйте их в файлы STL. Затем поместите детали в программное обеспечение Makerware и разложите детали, которые необходимо распечатать (корпус корпуса, шестерни, монтажная деталь, защелки, ручка направления, углубления для подлокотника *). Если детали не помещаются на станине принтера, дождитесь повторной печати. При печати не забудьте добавить опоры и подставки, чтобы предотвратить разрушение отпечатков.
Детали, вырезанные лазером: Используя акрил размером 18 на 24 дюйма, можно изготовить переднюю и заднюю пластины внешнего кожуха корпуса. Это можно сделать, взяв лицевую сторону обеих пластин в SolidWorks и сохранив их как файл DWG. Затем их можно загрузить в программное обеспечение для лазерной резки (в данном случае Epilog), в котором можно настроить их ориентацию, как показано на изображении. Из акрила будут вырезаны по две штуки, а из оставшегося материала будут вырезаны два прямоугольника. Прямоугольники будут служить подлокотниками.
Детали, вырезанные вручную: возьмите трубы и разрежьте их на части разной длины (две по 4,5 дюйма для ручки, две по 4,5 дюйма для соединения, две по 6,5 дюймов для рычага и две по 13,25 дюйма для руки). Оттуда отрежьте 13,25-дюймовые части рычага на одном конце (30 или 35 мм) посередине другой стороны трубы и просверлите отверстие 1/4 дюйма в 15 мм от краев трубы. Вырежьте и просверлите два отверстия. Соединительные детали диаметром 4,5 дюйма аналогичным образом, но с обеих сторон соединительной трубы из ПВХ. Проделайте то же самое (вырежьте и просверлите) с одной стороны плеча рычага, трубы диаметром 6,5 дюйма.
* Можно использовать выемки для подлокотника или весь подлокотник из предыдущего шага.
Шаг 14: Соберите все части вместе
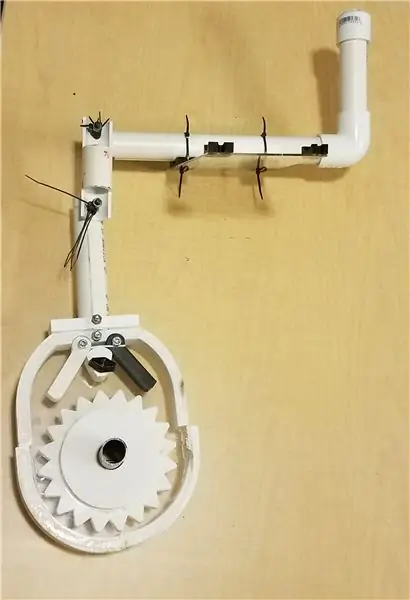
Сборка корпуса:
Возьмите вырезанные лазером внешние части тела и части корпуса, напечатанные на 3D-принтере. Возьмите одну сторону внешнего кожуха и приклейте детали кожуха соответственно краям кожуха. После этого возьмите резинку и оберните ею две собачки. Поместите собачки в соответствующие места, используйте болт с частичной резьбой и проденьте его через отверстие в корпусе и собачки. После этого возьмите ручку направления и пластиковую ручку. Проденьте пластиковую ручку через внешний кожух и скрутите их вместе с внешним кожухом между ними. Наконец, поместите шестерню в соответствующее отверстие, поместите верхнюю крышку внешнего кожуха на шестерню и приклейте кожух к верхнему внешнему кожуху. Дайте ему высохнуть. Не забудьте также закрепить два болта с частичной резьбой шестигранными гайками после установки и приклеивания верхней крышки к корпусу.
Возьмите 6,5-дюймовую рычажную трубку из ПВХ и приклейте ее к нижней стороне корпуса. Затем дайте ему высохнуть. Возьмите установленную деталь и протяните ее через трубу, пока она не приляжет ровно на нижнюю поверхность корпуса. Возьмите сверло диаметром 1/4 дюйма и просверлите отверстия в трубе и сквозь корпус в соответствующих местах. Закрепите болты шестигранной гайкой.
Сборка подлокотника:
С помощью подлокотника просто поместите и приклейте выемки на 4 углах подлокотника. Затем просверлите два отверстия (5/32 дюйма) с каждой стороны углублений и проденьте через них стяжки. Затем большие выемки можно совместить с 13-дюймовой трубкой из ПВХ и прикрепить к ней. Меньшая выемка должна быть выровнена, а затем прикреплена к подлокотнику кресла-коляски перед использованием.
Сборка рычага:
Наденьте колпачок на трубку с ручкой диаметром 4,5 дюйма и надежно поместите колено с другой стороны. В другое отверстие колена поместите 13-дюймовую трубку рукава и присоедините ее к одной стороне соединения (4,5-дюймовая труба) с помощью болта с буртиком. На другой стороне шарнира возьмите другой болт с буртиком и соедините его с рычагом (труба 6,5 дюйма). Возьмите шестигранную гайку и закрепите болт с буртиком. Поскольку болты с буртиком имеют частичную резьбу, соединения, в которых они крепятся, могут быть непрочными. Чтобы сделать соединения более плотными и надежными, оберните около пяти молний вокруг каждого плечевого болта, чтобы затянуть каждое соединение.
Шаг 15: Итеративное тестирование
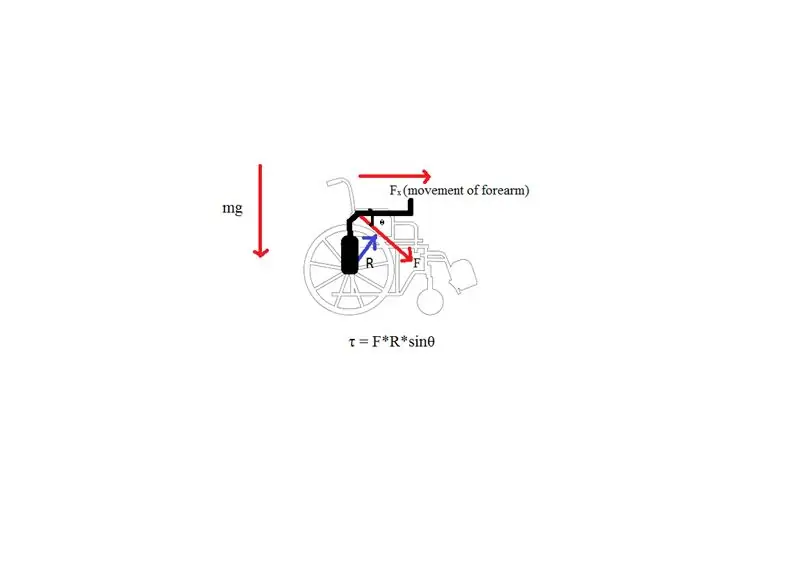
Для проверки убедитесь, что у вас есть доступ к одной из инвалидных колясок.
Присоедините рычаг к колесу. Убедитесь, что части подходят туда, где они должны быть, и убедитесь, что некоторые части параллельны соответствующим частям инвалидной коляски, например, подлокотнику. Убедитесь, что отверстия в алюминиевой трубе и корпусе рычага совмещены. Если детали непропорциональны, вернитесь назад и измените размеры.
Как только размеры и соотношения будут правильными, попросите тестировщика сесть в кресло-коляску и используйте рычаг. Как показано на диаграмме свободного тела, тестер будет продвигаться вперед по горизонтали, чтобы создать диагональную силу, которая будет использоваться для создания крутящего момента и продвижения кресла-коляски вперед. Проанализируйте любые проблемы: непрочность соединения, избыток или недостаток горизонтального пространства, поломки деталей и т. Д.
Проанализируйте проблемы и снова измените дизайн.
В нашем прототипе кресло-коляска двигалось, но медленно. Часть корпуса не успела приклеить, поэтому во время нашего пробного запуска сломалось плечо рычага. Кроме того, соединение могло быть слишком большим и неплотным, и на плече рычага могло не быть достаточного количества горизонтального пространства и движения, что ограничивало силу, прилагаемую к одному толчку.
Шаг 16: Страница вкладов
Индивидуальные взносы в систему поддержки
Руководитель проекта: София Инами 12732132
- Менеджер проекта, София Инами, отвечала за то, чтобы каждый член группы отвечал за свои обязанности и чтобы все задачи выполнялись своевременно. Я помогал в процессе окончательной сборки, а также тестировал и настраивал устройство перед окончательным запуском.
Производитель: Yvonne Szeto 94326050
- Производитель, Ивонн Сзето, отвечала за подготовку различных компонентов к сборке. Я отвечал за лазерную резку сырья, просверливание и 3D-печать различных деталей. Я также собрал вместе разные компоненты.
Инженер по материалам: Уиллис Лао 15649487
- Инженер по материалам, Уиллис Лао, отвечал за принятие решения о том, какие материалы использовать для каждого компонента проекта, и за их заказ / подборку в McMaster Carr / Home Depot. Я также внес свой вклад в Instructables, написав введение, анализ затрат, пошаговый процесс создания деталей и сборку.
Тестер: Мэтью Маравилла 25352925
- Тестировщик Мэтью Маравилла отвечал за надзор и анализ метода итеративного тестирования, включая тестирование плеча рычага и составление отчетов об изменениях размеров или деталей, подлежащих корректировке. Я также отвечал за набросок и большинство инструкций.
Ведущий дизайнер: Энтони Чеук 30511803
- Ведущий дизайнер Энтони Чеук отвечал за разработку осуществимого дизайна с учетом различных материалов, которые можно было использовать, и за подготовку файлов и дизайна к производству (3D-печать и лазерная резка).
Рекомендуемые:
D4E1 - Сделай сам - Вспомогательные технологии: регулируемый поднос для инвалидной коляски: 7 шагов (с изображениями)
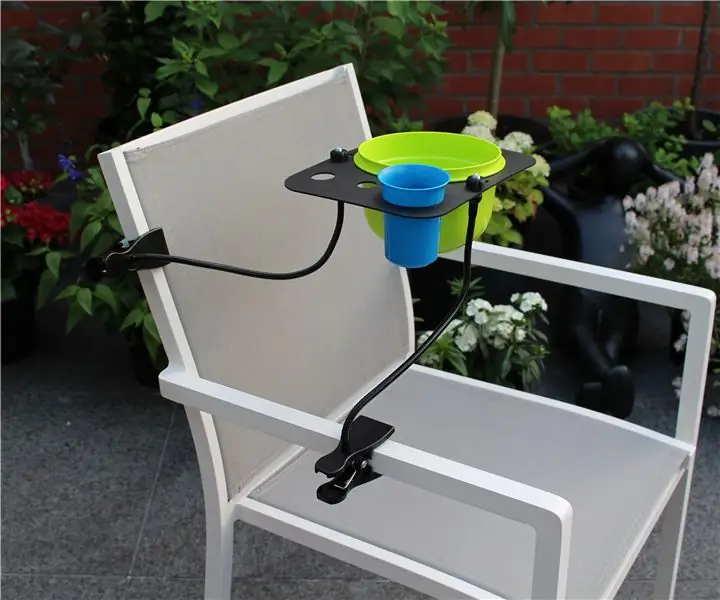
D4E1 - Сделай сам - Вспомогательные технологии: регулируемый поднос для инвалидной коляски: Кьелл имеет врожденную инвалидность: дискинетический квадрипарез и не может самостоятельно есть. Ему нужна помощь наблюдателя, эрготерапевта, который его кормит. Здесь возникают две проблемы: 1) Эрготерапевт стоит за рулем
Отчет - Монитор производительности водителя: 5 шагов
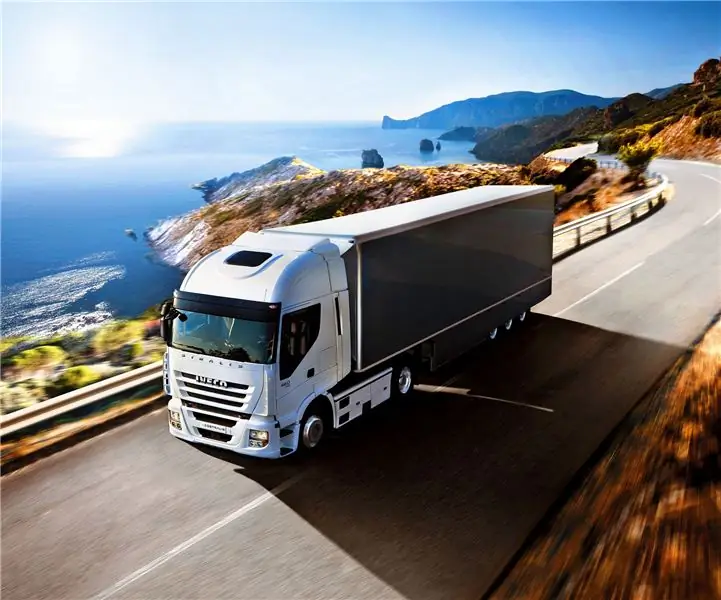
Отчет - Монитор производительности драйвера: Отчет !? Что это такое? Это электронное устройство, которое собирает данные с грузовиков в режиме реального времени и использует их для создания отчета о том, как грузовик вел себя во время поездки, показывая это на платформе Iot для менеджеров автопарка. Наша цель - сотрудничать
Вязание крючком для инвалидной коляски: 18 шагов
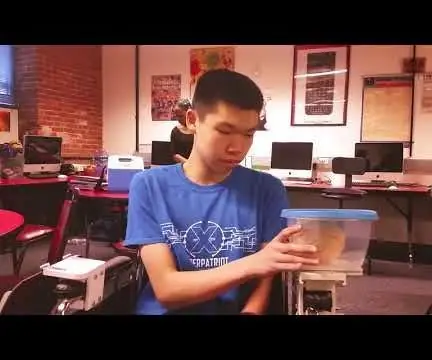
Вязание крючком для инвалидной коляски: человек с приобретенной черепно-мозговой травмой, который не может использовать одну из рук, испытывает трудности с удержанием пряжи для вязания крючком. Ей также трудно дозировать пряжу, чтобы она не запуталась в инвалидной коляске. Вязание - это
Камера заднего вида для электрической инвалидной коляски: 10 шагов (с изображениями)
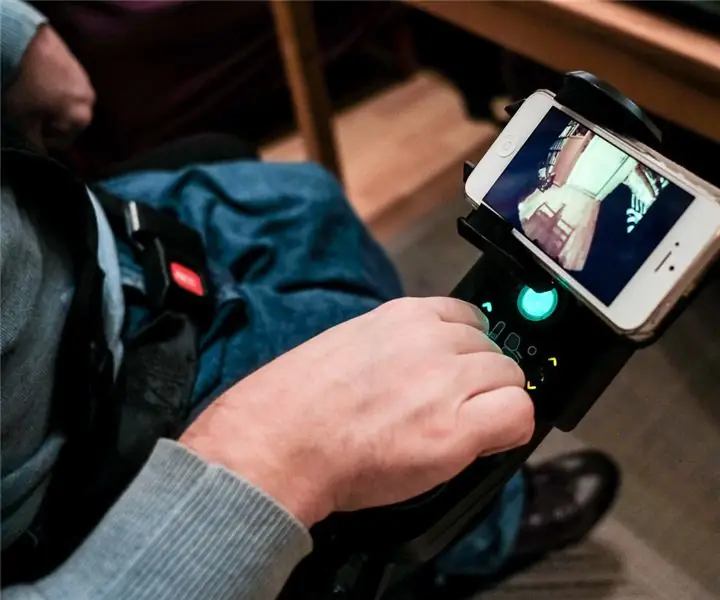
Камера заднего вида для электрической инвалидной коляски: Мой брат использует электрическую инвалидную коляску Invacare TDX, которая легко маневрирует во всех направлениях, но из-за ограниченной видимости сзади на ограниченном пространстве трудно ехать назад. Цель проекта - построить камеру заднего вида
Снятие моторного тормоза инвалидной коляски: 6 шагов (с изображениями)
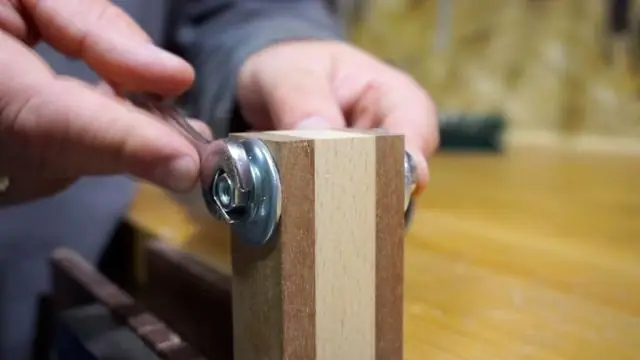
Снятие моторного тормоза для инвалидной коляски: снятие электрического предохранительного тормоза с мотора для инвалидной коляски - это быстро и легко. Эти инструкции предназначены для людей, которые надеются повторно использовать двигатель инвалидной коляски для проектов DIY. Отключение предохранительного тормоза делает управление электрическим