
Оглавление:
2025 Автор: John Day | [email protected]. Последнее изменение: 2025-01-23 15:05
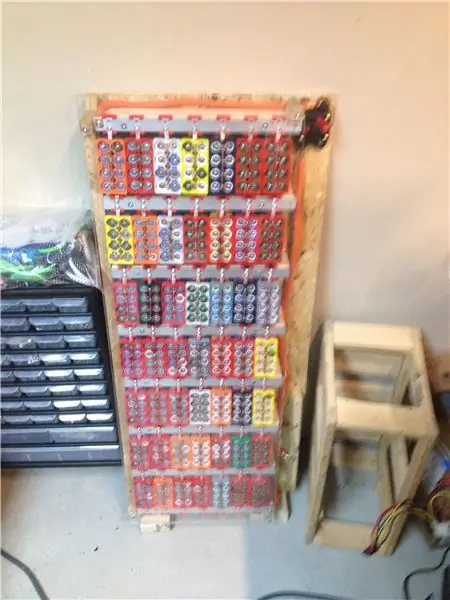
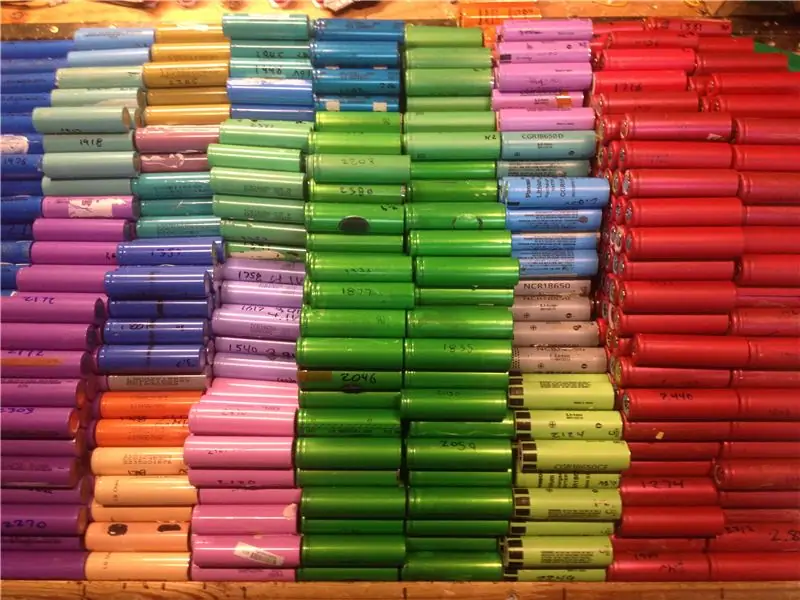
Мой Powerwall мощностью 2,4 кВт, наконец, готов!
За последние несколько месяцев у меня накопилось много аккумуляторов 18650 для ноутбуков, которые я тестировал на своей тестовой станции DIY 18650, поэтому я решил что-то с ними сделать. Некоторое время я слежу за некоторыми сообществами DIY powerwall, поэтому я решил создать такое.
Это мой взгляд на небольшой Powerwall.
Вы также можете просмотреть этот проект на моем сайте здесь:
a2delectronics.ca/2018/06/22/2-4kwh_diy_po…
Шаг 1. Начало работы с держателями
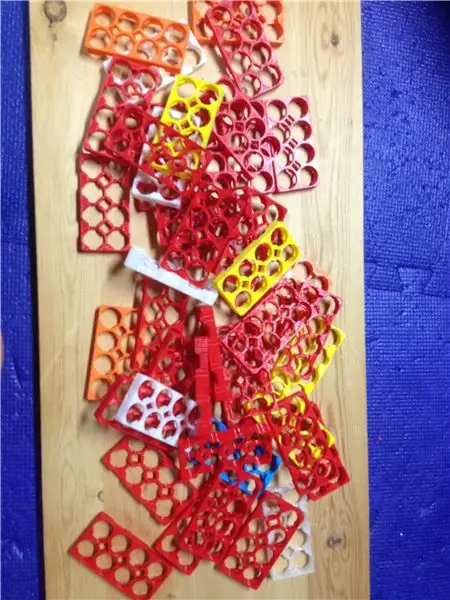
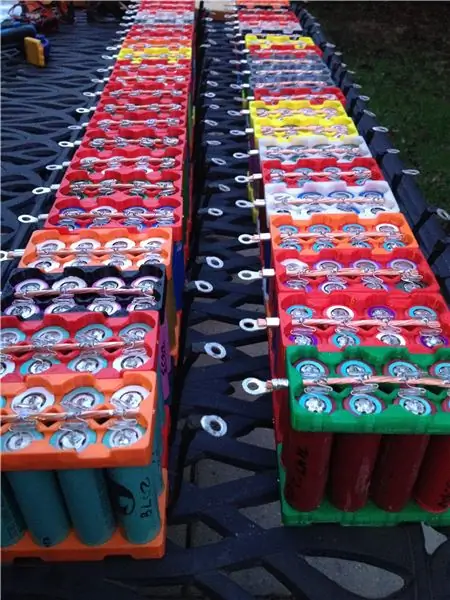
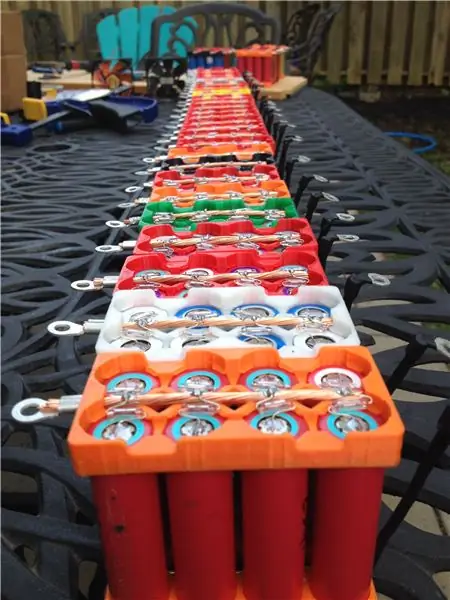
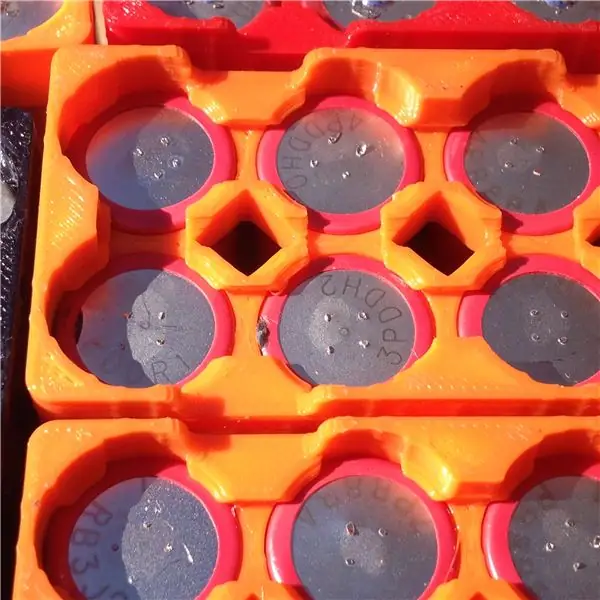
Я разработал около 8 держателей ячеек, чтобы можно было легко менять небольшие участки ячеек.
Печать держателей заняла много времени, и, к счастью, мне помог друг с печатью. Мне пришлось распечатать почти 100 держателей, используя чуть больше полного рулона нити.
Затем пришла основная тяжесть работы - было выполнено более 1500 паяных соединений для этой сборки (это заняло некоторое время). Я паял большую часть на улице, потому что там намного лучше вентиляция и хорошая погода, так почему бы не воспользоваться этим?
Положительный конец каждой ячейки был припаян к предохранителю на 4А. Я выбрал 4A, поскольку эта электрическая стена также была разработана для управления электромобилем, над которым я работал для Waterloo EV Challenge с EVPioneers. и должен был иметь возможность подавать импульсный ток 150 А. У меня было достаточно предохранителей на 2А и 4А, а 2А не давали мне достаточной мощности. Для использования в качестве силовой стены я бы рекомендовал использовать предохранители на 1 или 2 А, потому что это будет удерживать элементы в разумных рабочих пределах. Да, большинство новых ячеек могут непрерывно работать с током 4А (2С), но после долгого срока службы ноутбуков безопаснее поддерживать их в непрерывном режиме с током 1С.
Шаг 2: Подключения сборных шин
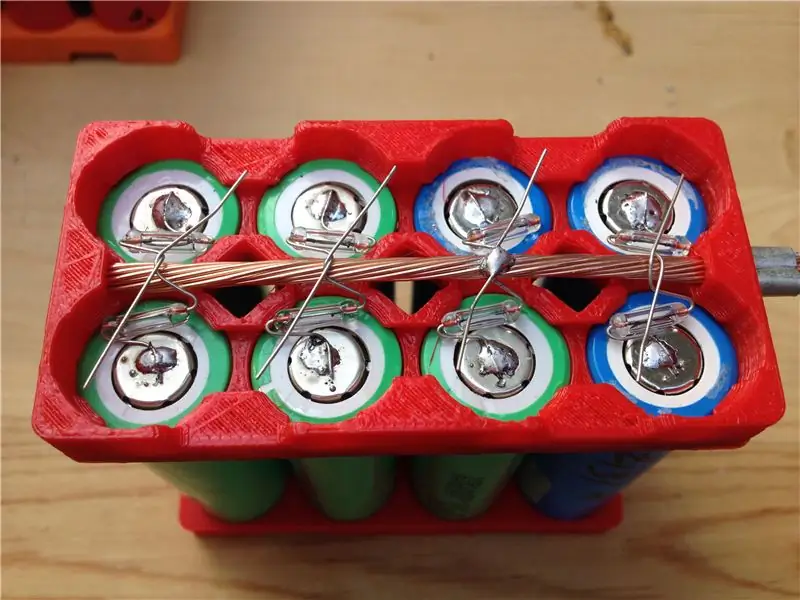
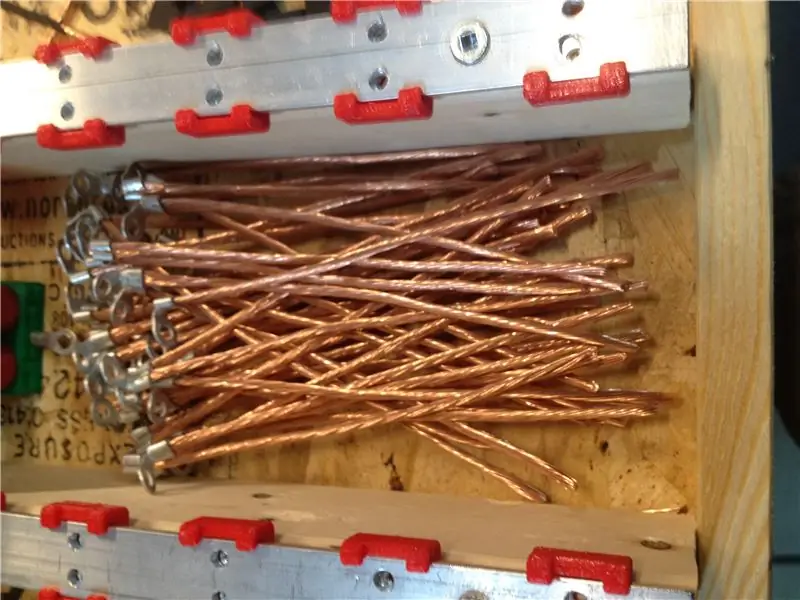
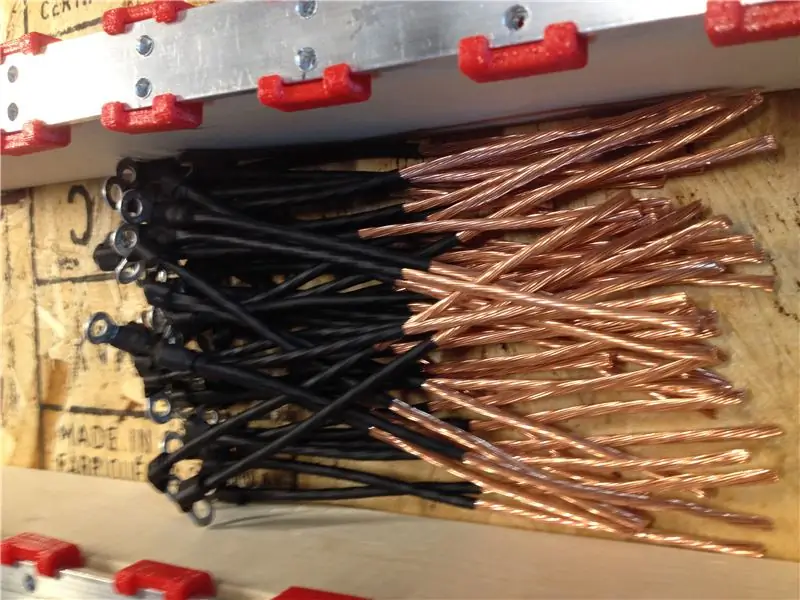
Отрицательный конец был подключен к шинам с дополнительными ножками провода предохранителя, которые были отрезаны от положительного конца, и это подводит меня к шинам. Первоначально я планировал использовать медь - либо плоские стержни из медных труб, но, проверив цены и осуществимость, я отказался от этого. Мне не удалось найти простой способ прикрепить 8-элементные модули к медным трубам без пайки, и, сравнивая цены на медные шины и алюминиевые шины, я выбрал алюминиевые шины размером 1/8 ″ * 3/4 ″.
Присоединение модулей с 8 ячейками к решеткам было еще одним приключением. На каждом из модулей с 8 ячейками предохранители были припаяны к проводу с винтовым зажимом на конце, чтобы можно было заменить модули с 8 ячейками без пайки. Первоначально я планировал использовать для этого провод 16AWG, но после проверки провода 12AWG, который у меня лежал, было намного легче снять изоляцию с провода 12AWG, и он меньше нагревается при больших нагрузках. На плюсовом конце я сделал провод немного длиннее, чем модули, чтобы они умещались в минимально возможном пространстве и имели достаточно места для обжима винтовой клеммы. Отрицательный конец получил провод, который был загнут до того же уровня, что и положительный. Я покрыл этот более длинный провод термоусадкой, насколько это было возможно, трех разных размеров, чтобы предотвратить его короткое замыкание, когда положительный конец просто высовывает конец, противоположный его винтовому зажиму.
Шаг 3: алюминиевые шины
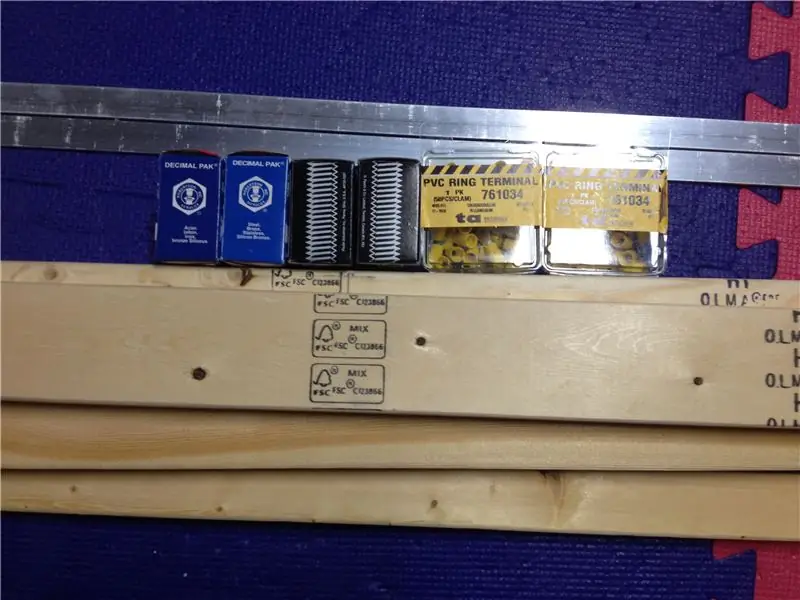
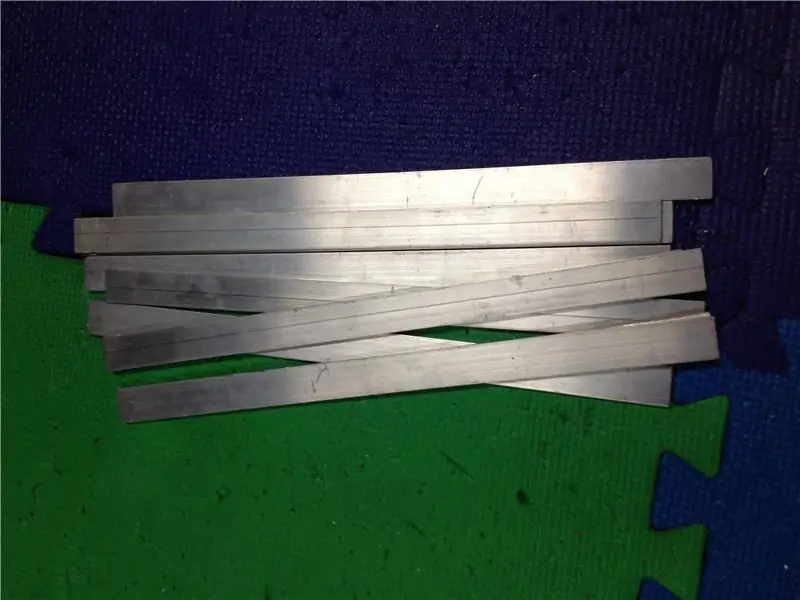
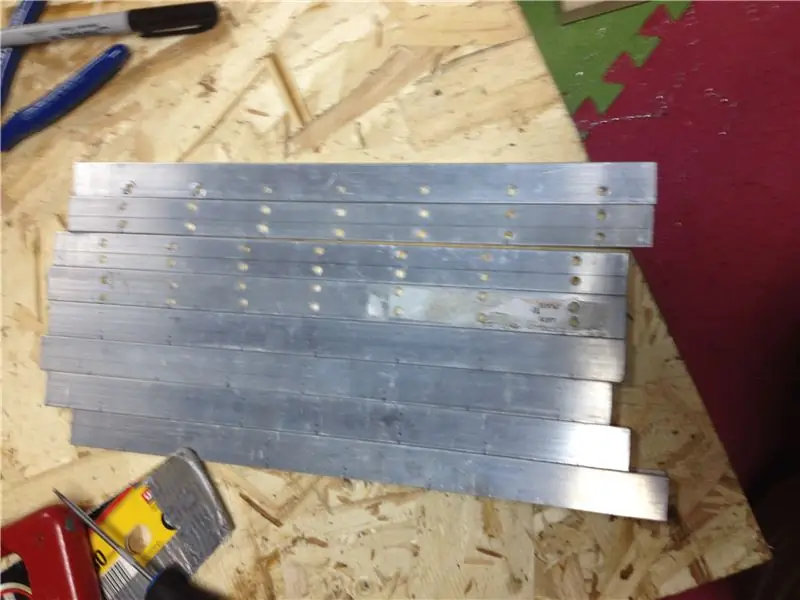
Теперь, чтобы на самом деле получить эти детали - поездка в строительный магазин за 70 долларов, я вернулся с 8-футовым алюминием, 100 винтовыми клеммами 12AWG, 200 гайками и болтами 6-32 (они были самыми дешевыми) и небольшим количеством дерева для рамы.
Я разрезал алюминий на отрезки длиной 1 фут, затем просверлил в нем много отверстий для крепления алюминия к раме силовой стены и для крепления винтовых клемм. Мне не хотелось вытаскивать плоскогубцы, чтобы удерживать гайки на месте, и рисковать закоротить что-нибудь при прикручивании пакетов к шинам, и я недавно видел, как Адам Велч делал несколько невыпадающих гаек на своем автобусе с солнечным навесом. бары. Поэтому я разработал аналогичную систему, которая будет удерживать 2 гайки. Распечатав 56 из них, я начал вставлять гайки и надевать их на алюминиевые шины.
Шаг 4: строительство каркаса
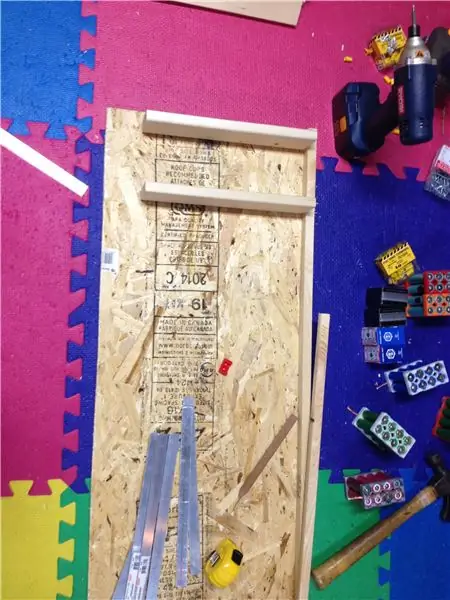
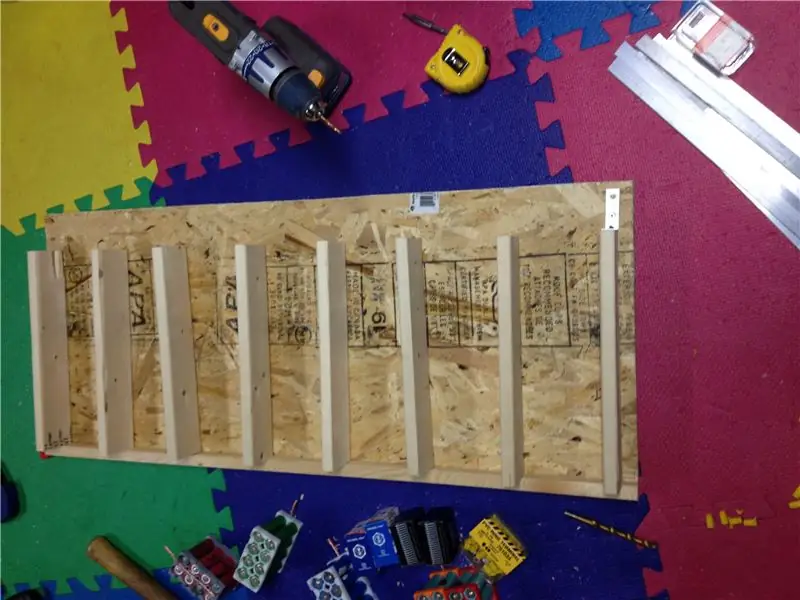
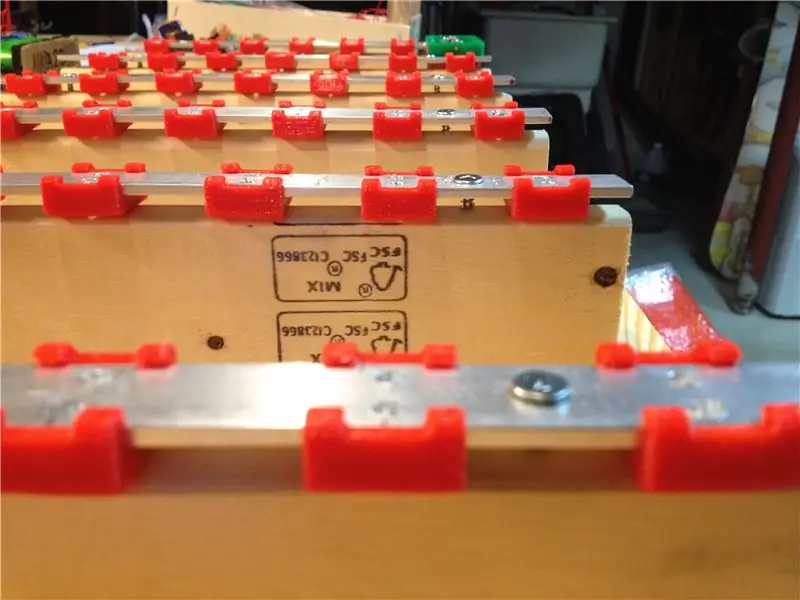
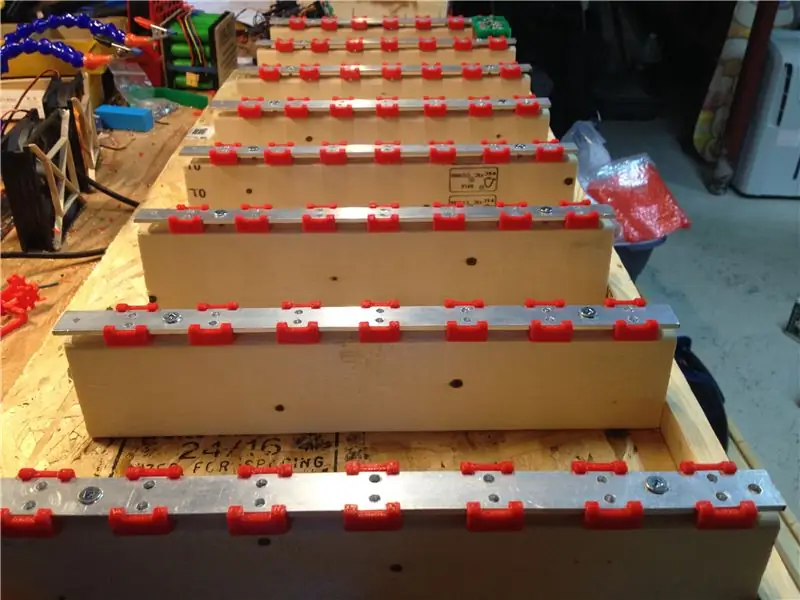
Каркас этой силовой стены сделан из дерева. Мне действительно следовало использовать что-то негорючее, чтобы все установить, но я не смог найти металлический шкаф или что-то подобное подходящего размера. Я также не хотел тратить 150 долларов на корпус, так что он деревянный. Я не думаю, что со всеми тестами, которые я провел на этих ячейках, и индивидуальным слиянием каждой из них. Я буду постоянно следить за этим в поисках нагревателей и проверять напряжение.
Каждая параллельная группа отделена куском 1 × 3, на который я установил алюминиевые шины. После того, как все 8 шин были смонтированы, я начал добавлять пакеты, балансируя мощности, насколько это было возможно. Я использовал ударный ключ, чтобы затянуть все винты - ранее я заменил стареющий никель-кадмиевый аккумулятор в ударном драйвере 18650, и он все еще отлично работает. Я наткнулся на один напечатанный на 3D-принтере держатель, который я снял, но, к счастью, он находился на конце одной из шин, так что его было легко заменить. В завершение я добавил автоматический выключатель на 150 А к положительному концу и добавил прозрачный акриловый лист толщиной 1/4 дюйма поверх батарей для предотвращения коротких замыканий.
Шаг 5: Заполнение и инвертор
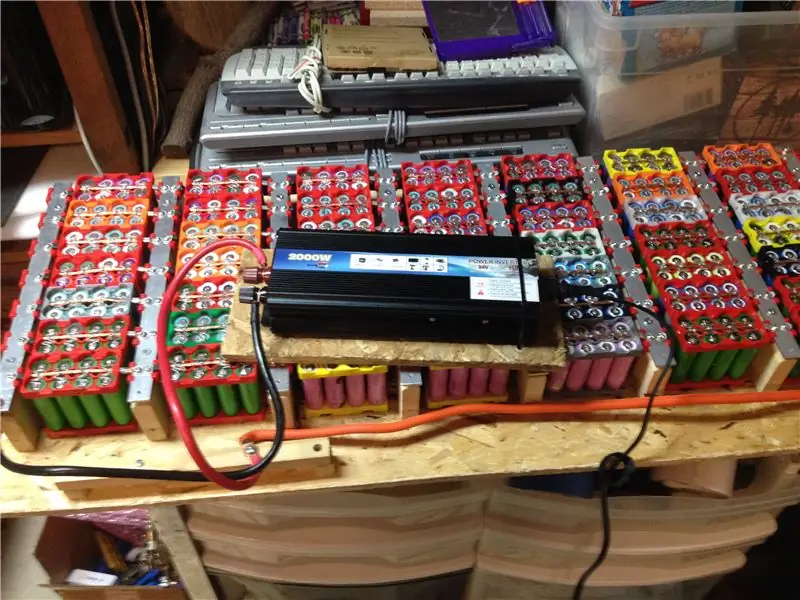
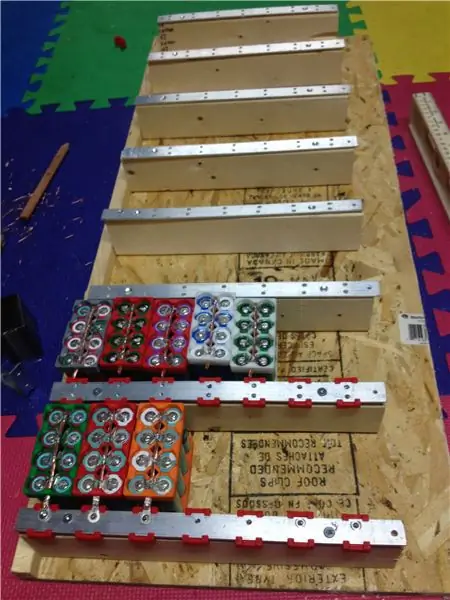
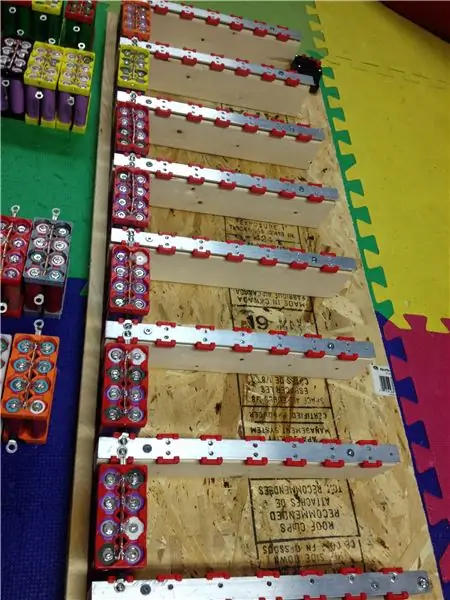
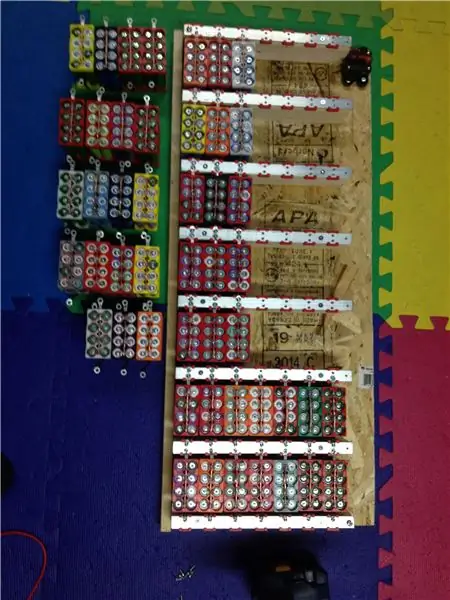
Инвертор, который я использовал для этого, представляет собой модифицированный синусоидальный инвертор мощностью 1000 Вт. Это был один из самых дешевых компонентов на Amazon, и, вероятно, это был бы тот компонент, который я бы изменил, если бы сделал это снова. С другой стороны, почти вся моя мастерская работает от постоянного тока, так что это не такая уж большая проблема. Мне он нравится, потому что он нагревает мой паяльник переменного тока мощностью 60 Вт лучше, чем домашний. Мой обычный паяльник - клон Hakko T12 - питается от постоянного тока, как и мои фонари, и в конечном итоге я добавлю в этот список свой 3D-принтер., но пока это было потрясающе.
Рекомендуемые:
Как получить 18650 клеток из разряженных аккумуляторов ноутбуков !: 7 шагов (с изображениями)
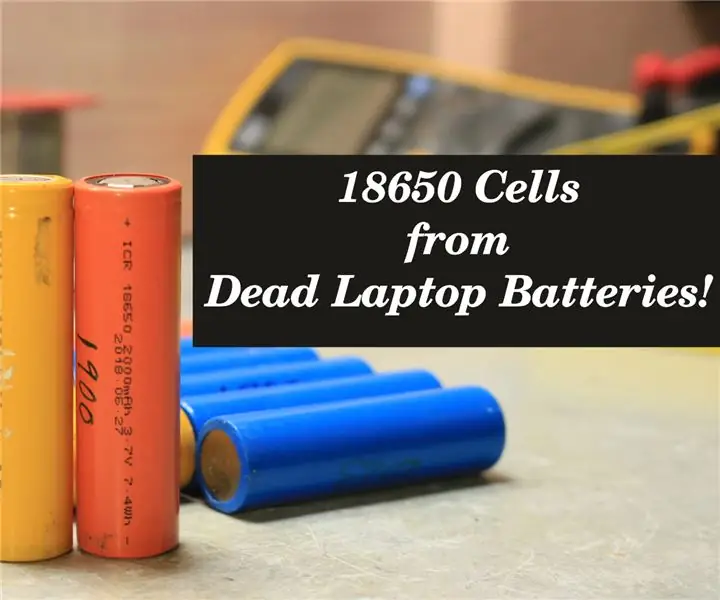
Как получить 18650 ячеек из разряженных аккумуляторов портативных компьютеров! Когда дело доходит до строительных проектов, мы обычно используем источник питания для прототипирования, но если это портативный проект, то нам нужен источник питания, такой как литий-ионные элементы 18650, но эти элементы иногда дорого или большинство продавцов не продают
Сделай сам PowerBank из старых аккумуляторов для ноутбуков: 7 шагов
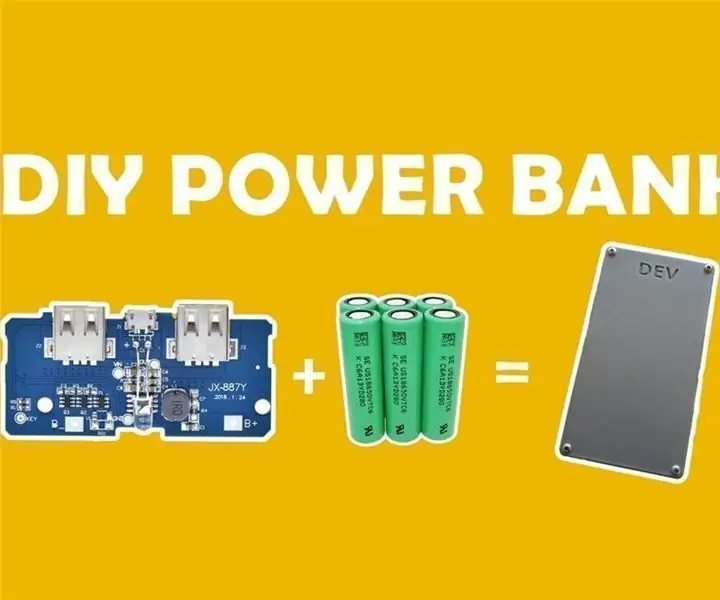
Сделай сам PowerBank из старых аккумуляторов для ноутбуков: в большинстве случаев первое, что повреждается от вашего ноутбука, - это аккумулятор, и в большинстве случаев могут быть неисправны только 1-2 элемента. У меня на столе лежит несколько батареек от старого ноутбука, поэтому я подумал сделать из них что-нибудь полезное
Банк солнечной энергии с использованием старых аккумуляторов для ноутбуков: 5 шагов
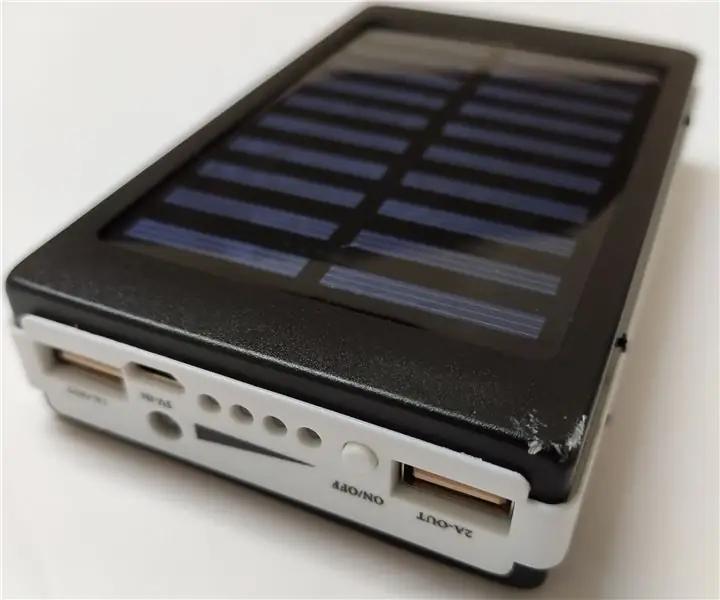
Solar Power Bank с использованием старых аккумуляторов для ноутбуков: Привет всем, в этой инструкции я расскажу, как сделать Solar Power Bank, используя комплект и старые аккумуляторы для ноутбуков. Этот комплект был куплен на Aliexpress. Внешний аккумулятор имеет светодиодную панель, которую можно использовать для кемпинга. такой хороший встроенный внешний аккумулятор и легкая комбинация
Повторное использование аккумуляторов для ноутбуков: 10 шагов
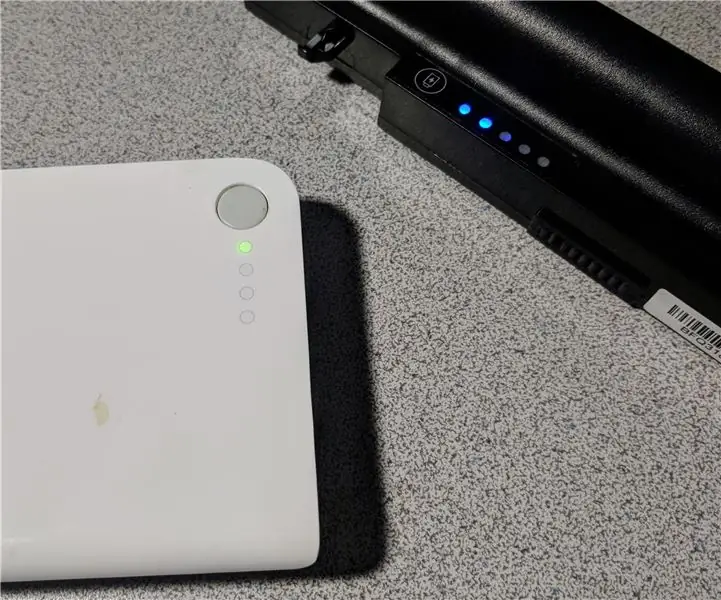
Повторное использование аккумуляторов для ноутбуков: почти неизбежно каждый хакер начнет собирать несколько аккумуляторов из старых ноутбуков. Несмотря на то, что некоторые из этих батарей начинают стареть и теряют способность накапливать заряд, они по-прежнему полезны для других проектов. Один из основных механизмов
Литий-ионный аккумулятор 280 Вт-ч 4S 10P, изготовленный из переработанных аккумуляторов для ноутбуков: 6 шагов (с изображениями)
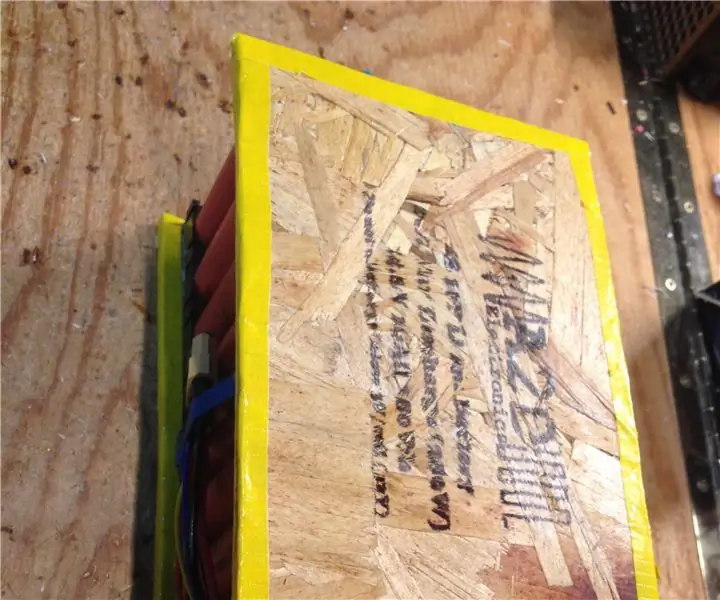
Литий-ионная батарея 280 Вт-ч 4S 10P, изготовленная из переработанных аккумуляторов для ноутбуков: в течение последнего года или около того я собирал аккумуляторы для ноутбуков, обрабатывал и сортировал элементы 18650 внутри. Мой ноутбук сейчас стареет, с i7 2dn gen, он жрет энергию, поэтому мне нужно было что-то, чтобы заряжать его на ходу, хотя при себе этот ба