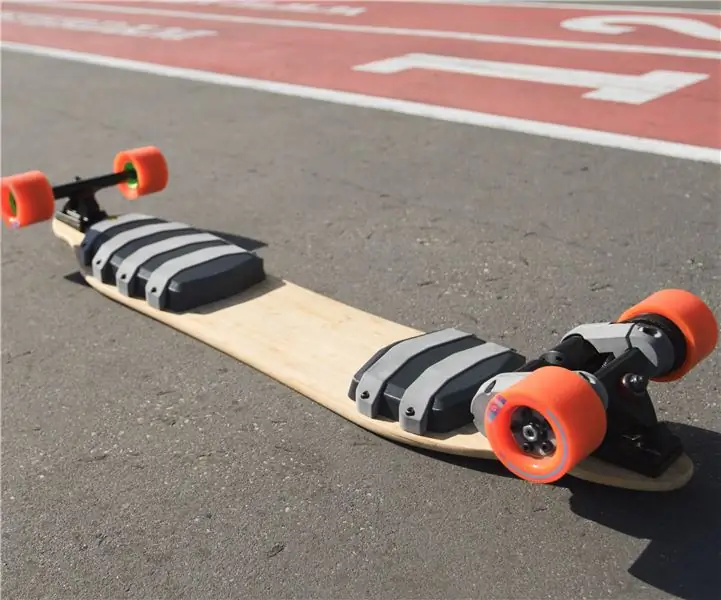
Оглавление:
2025 Автор: John Day | [email protected]. Последнее изменение: 2025-01-23 15:05
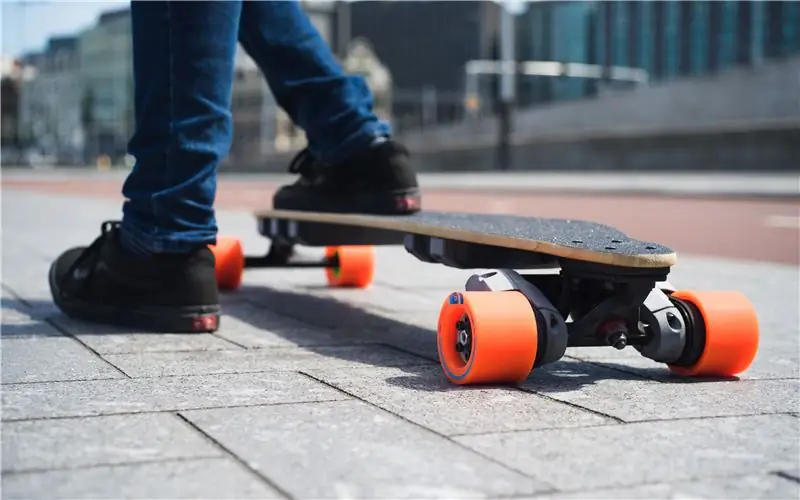
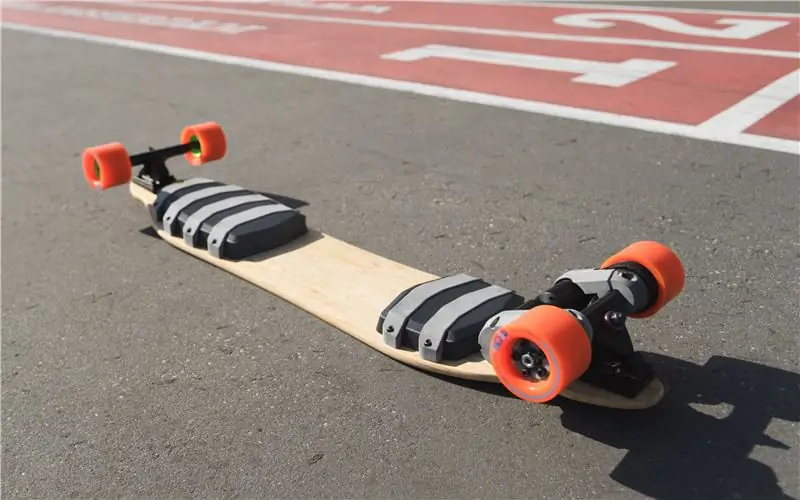
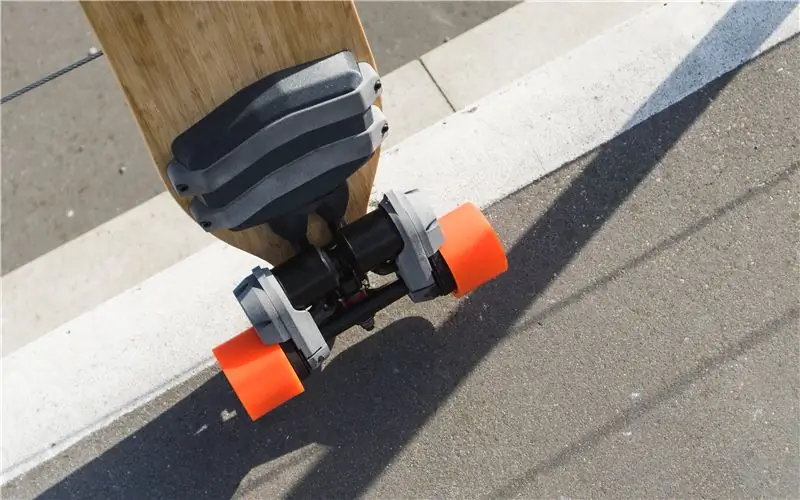
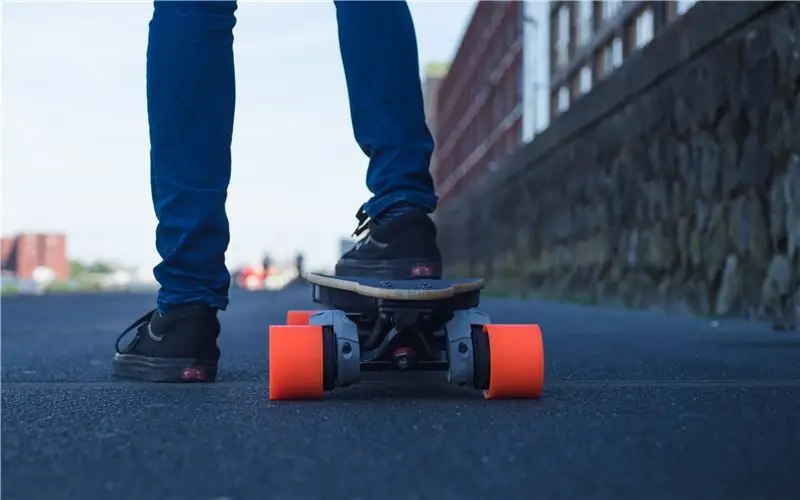
Это руководство представляет собой обзор процесса сборки Fusion E-Board, который я спроектировал и построил, работая в 3D Hubs. Проект был заказан для продвижения новой технологии HP Multi-Jet Fusion, предлагаемой 3D Hubs, а также для демонстрации нескольких технологий 3D-печати и того, как их можно эффективно комбинировать.
Я спроектировал и построил лонгборд с электродвигателем, который можно использовать для коротких и умеренных поездок или в сочетании с общественным транспортом, чтобы предложить гораздо более широкий диапазон путешествий. Он имеет высокую максимальную скорость, очень маневренный и легко переносится, когда не используется.
Шаг 1: процесс проектирования
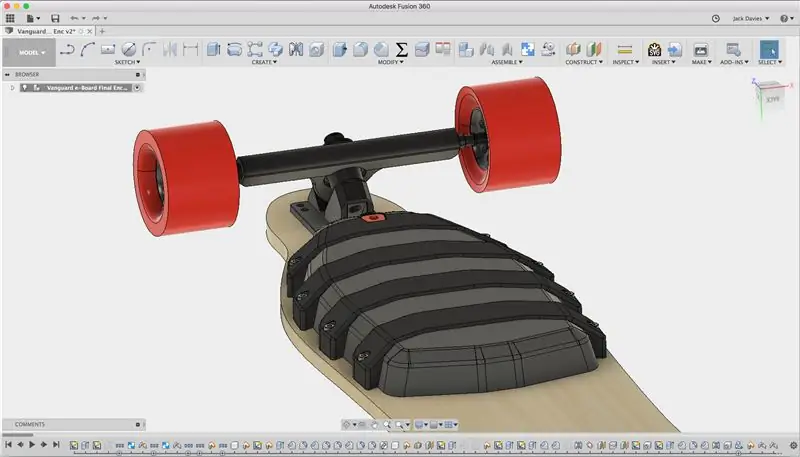
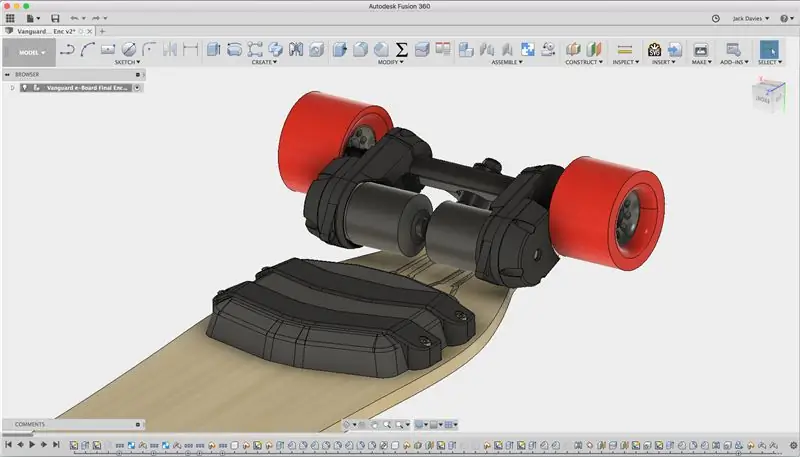
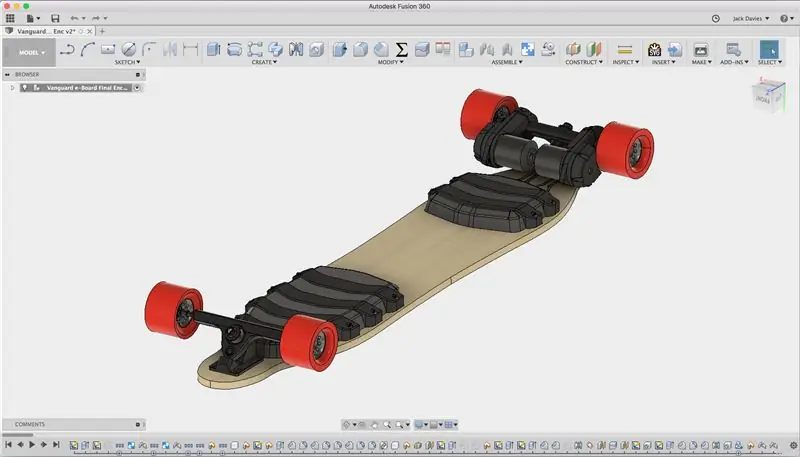
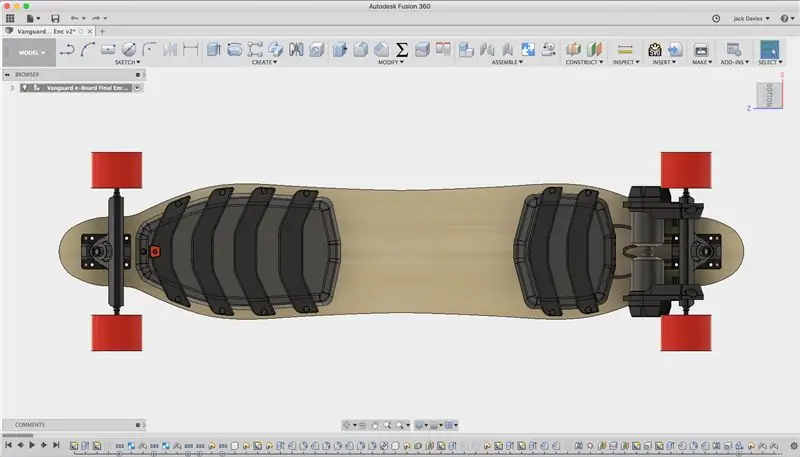
Я начал проект с определения основных стандартных компонентов лонгборда; грузовики, палуба и колеса. Это были готовые детали, поэтому я использовал их как отправную точку дизайна. Первым этапом было проектирование трансмиссии, включая опоры двигателя, установку зубчатой передачи и некоторые модификации грузовиков. Размер и положение опор двигателя будут определять размер и расположение корпусов, поэтому было важно, чтобы это было выполнено в первую очередь. Я рассчитал желаемую максимальную скорость и требования к крутящему моменту, что позволило мне выбрать двигатели и аккумулятор для платы. Также было рассчитано передаточное число и выбраны размеры шкивов и длина приводного ремня. Это позволило мне определить правильный размер опор двигателя, обеспечивающий хорошее натяжение ремня.
Следующим этапом было проектирование корпусов аккумуляторной батареи и регулятора скорости (ESC). Выбранная колода в основном состоит из бамбука, поэтому она довольно гибкая и сильно изгибается посередине. У этого есть преимущества в том, что он удобен для езды, поскольку он поглощает неровности дороги и не передает их водителю. Однако это также означает, что для размещения батареи и электроники необходим раздельный корпус, поскольку корпус во всю длину не сможет сгибаться с платой и будет контактировать с землей во время работы. Электронные регуляторы скорости (ESC) были размещены ближе всего к двигателям из-за электрических ограничений. Поскольку двигатели прикреплены с помощью тележек, положение меняется во время поворотов, поэтому необходимо было спроектировать кожух с учетом зазора между двигателями.
Система батарей была размещена на другом конце палубы и в ней размещалась электроника, связанная с питанием. Это включало аккумуляторный блок, состоящий из 20 литий-ионных элементов 18650, систему управления аккумулятором, переключатель включения / выключения и гнездо для зарядки.
Я использовал Autodesk Fusion360 для всего процесса проектирования, это программное обеспечение позволило мне быстро моделировать компоненты внутри основной сборки, что значительно ускорило время разработки. Я также использовал функции моделирования в Fusion360, чтобы убедиться, что детали будут достаточно прочными, особенно крепления двигателя. Это позволило мне фактически уменьшить размер опор, поскольку я мог проверить требования к прочности и прогибу и удалить материал, сохраняя при этом соответствующий коэффициент безопасности. После завершения процесса проектирования стало очень легко экспортировать отдельные детали для 3D-печати.
Шаг 2: трансмиссия
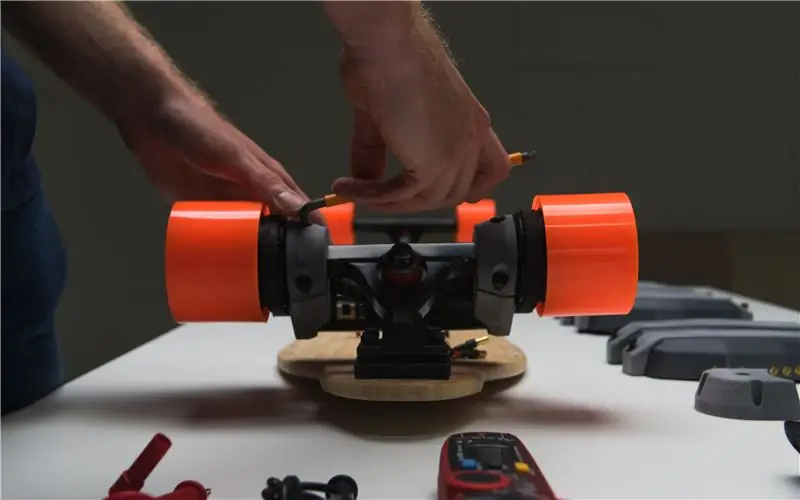
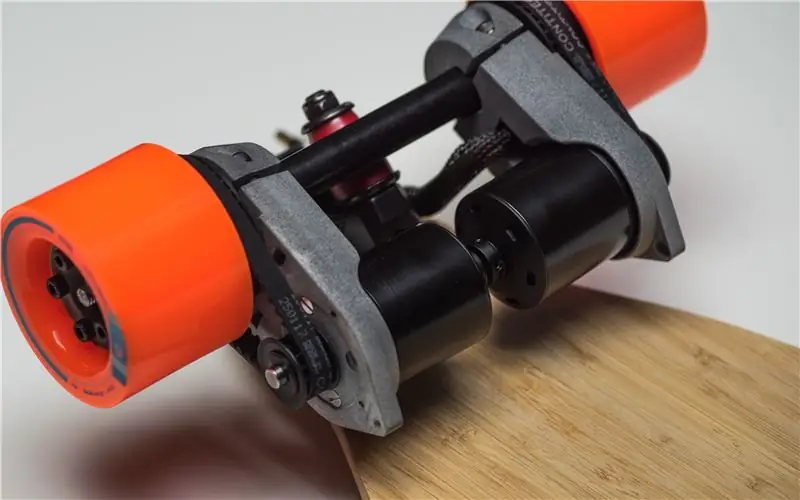
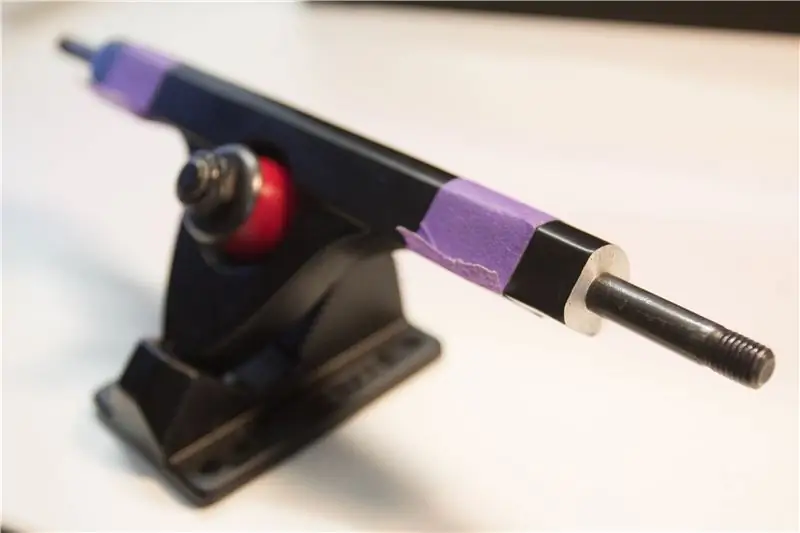
Сначала я завершил сборку трансмиссии, чтобы обеспечить необходимый зазор для корпуса электроники. Я выбрал грузовики Caliber для использования, так как они имеют квадратный профиль, который идеально подходит для крепления опор двигателя. Однако ось была немного слишком короткой, чтобы можно было использовать два двигателя на одном грузовике, поэтому мне пришлось удлинить ее, чтобы колеса поместились.
Я добился этого, срезав часть алюминиевого кузова подвески грузовика, обнажив большую часть стальной оси. Затем я обрезал большую часть оси, оставив около 10 мм, которые затем можно было продеть с помощью штампа M8.
Затем можно было навинтить муфту и добавить к ней еще одну ось с резьбой, эффективно удлиняющую ось. Я использовал фиксирующий состав Loctite 648, чтобы надежно закрепить муфту и новую ось, чтобы они не открутились во время использования. Это позволило двум двигателям поместиться на грузовике и обеспечило достаточный зазор для колес.
Трансмиссия была в первую очередь напечатана с использованием технологии HP Multi-Jet Fusion, чтобы обеспечить жесткость и прочность во время высоких ускорений и торможений, где будут передаваться самые большие силы.
Для фиксации задних колес был разработан специальный шкив, который затем соединялся со шкивом двигателя с помощью ремня HTD 5M. Для защиты узла шкива была добавлена крышка, напечатанная на 3D-принтере.
Шаг 3: ребристые корпуса
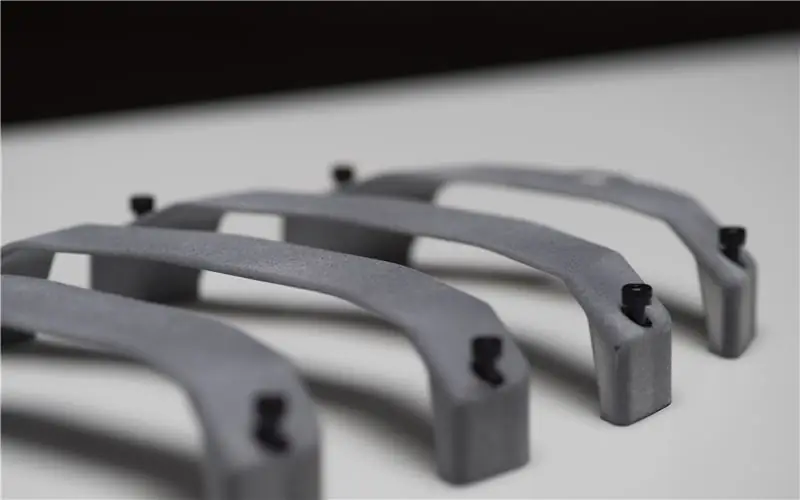
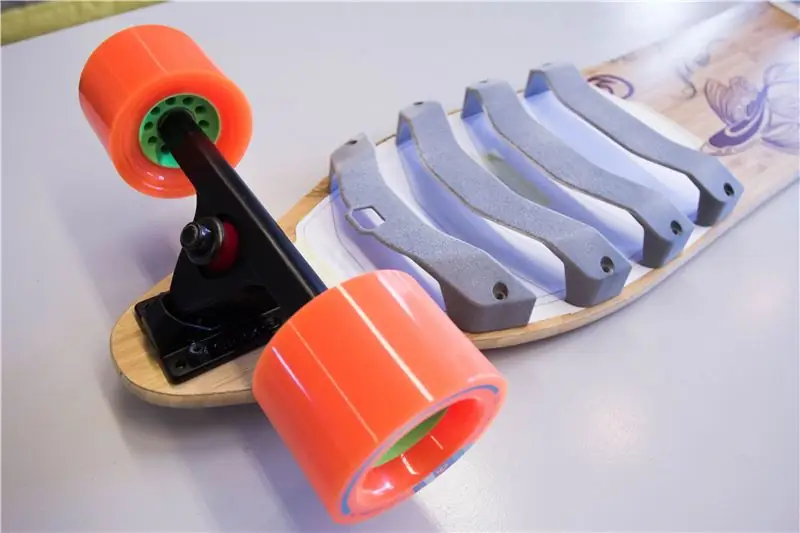
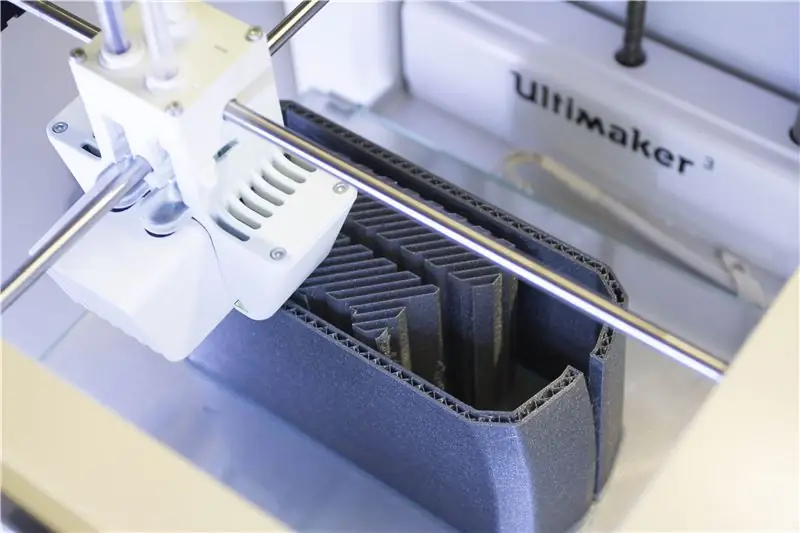
Одним из основных дизайнерских решений, которые я принял, было разделение корпусов, что привело к чистому виду и позволило гибкой платформе функционировать без какой-либо дополнительной жесткости со стороны корпусов. Я хотел передать функциональные аспекты технологии HP Multi Jet Fusion, поэтому решил напечатать с помощью FDM основную часть корпуса, что снизило затраты, а затем использовал детали HP для поддержки и фиксации их на платформе. Это обеспечило интересную эстетику, но при этом было очень функционально.
Корпуса с печатью FDM были разделены пополам, чтобы облегчить печать, поскольку материал основы можно было удалить с внешней поверхности. Линия разделения была тщательно расположена, чтобы гарантировать, что она будет скрыта частью высокого давления при закреплении на плате. Были добавлены отверстия для соединений двигателя и приклеены позолоченные соединители для пуль.
Резьбовые вставки были встроены в бамбуковую платформу, чтобы прикрепить кожухи к плате, и отшлифованы заподлицо с поверхностью платы, чтобы гарантировать отсутствие зазора между декой и кожухом.
Шаг 4: Электроника
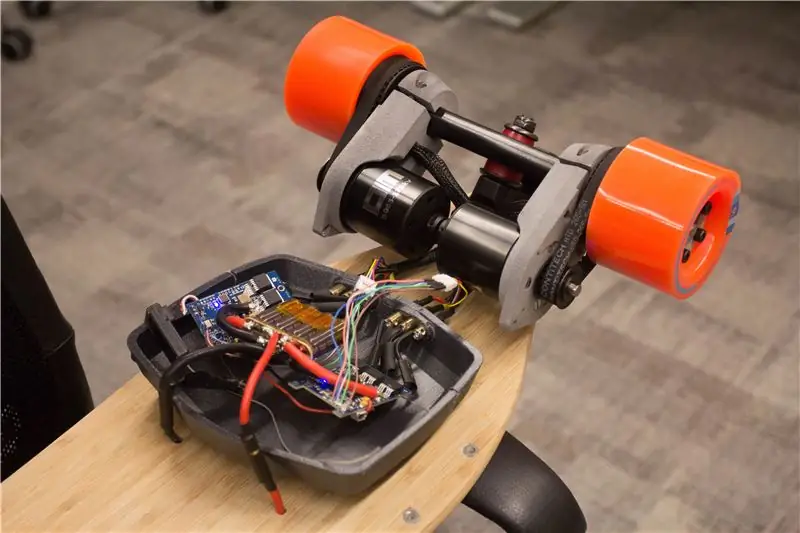
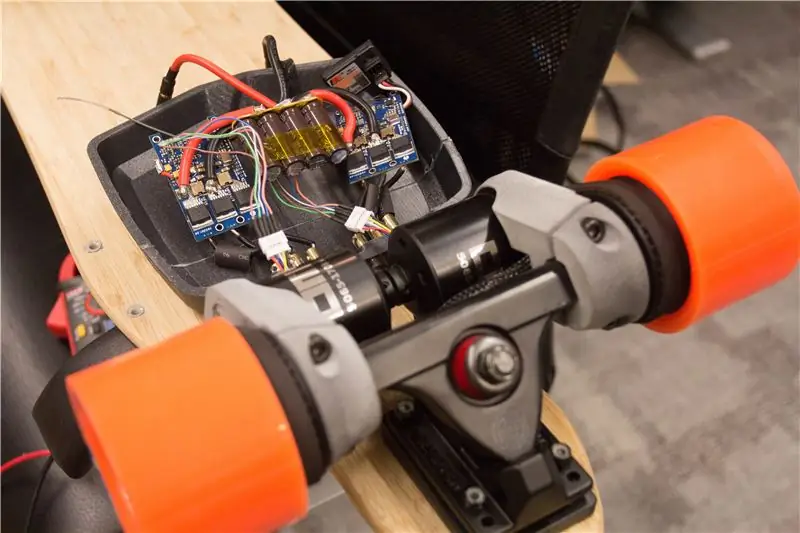
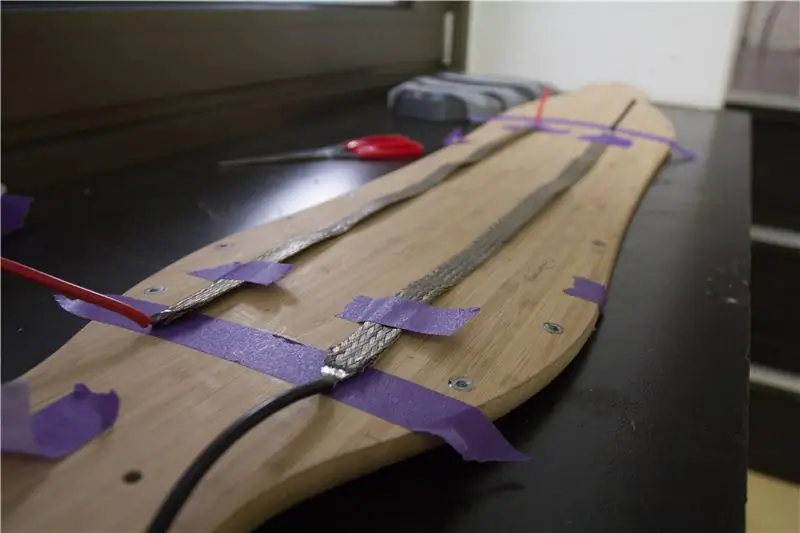
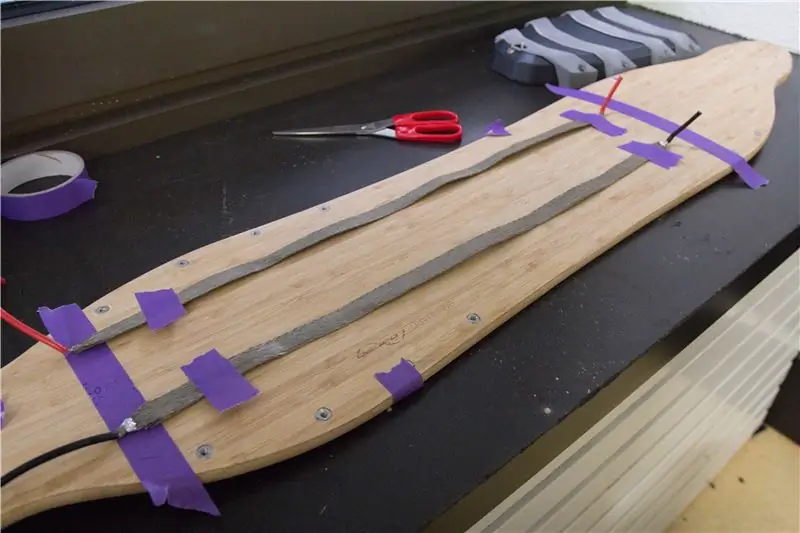
Электроника была тщательно выбрана, чтобы плата была мощной, но в то же время интуитивно понятной в использовании. Эта плата может быть потенциально опасной в случае возникновения каких-либо неисправностей, поэтому надежность является очень важным фактором.
Батарейный блок состоит из 20 отдельных литий-ионных элементов 18650, которые сварены точечной сваркой, образуя блок на 42 В. 2 ячейки привариваются параллельно и 10 последовательно; Я использовал ячейки Sony VTC6. Я использовал точечную сварку, чтобы сварить никелевые выступы, чтобы сформировать пакет, так как при пайке выделяется слишком много тепла, которое может повредить элемент.
Электропитание от батарейного отсека передавалось на блок регулятора скорости с помощью плоского плетеного кабеля, который проходил прямо под лентой для захвата на верхней стороне деки. Это позволяло «спрятать» кабели и избавляло от необходимости прокладывать кабели на нижней стороне, что выглядело бы некрасиво.
Поскольку это плата с двумя двигателями, для независимого управления каждым двигателем требуются два регулятора скорости. Я использовал контроллер скорости VESC для этой сборки, который является контроллером, специально разработанным для электрических скейтбордов, что делает его очень надежным для этого использования.
Используемые двигатели - это выдвижные двигатели мощностью 170 кВт 5065, каждый из которых может производить 2200 Вт, что является большой мощностью для этой платы. При текущей настройке передачи максимальная скорость платы составляет около 35 миль в час, и она ускоряется очень быстро.
Последним этапом было создание пульта для управления платой. Предпочтение было отдано беспроводной системе из-за более легкого управления. Однако было важно обеспечить высокую надежность передачи, поскольку прерывание связи могло иметь серьезные проблемы с безопасностью, особенно на высоких скоростях. После тестирования нескольких протоколов радиопередачи я решил, что радиочастота 2,4 ГГц будет наиболее надежной для этого проекта. Я использовал стандартный радиоуправляемый автомобильный передатчик, но значительно уменьшил его размер, перенеся электронику в небольшой переносной футляр, который был напечатан на 3D-принтере.
Шаг 5: Готовая доска и промо-видео
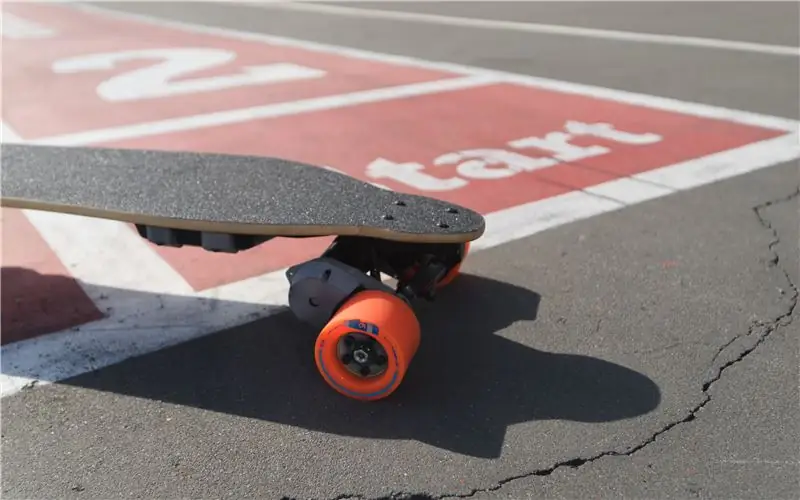
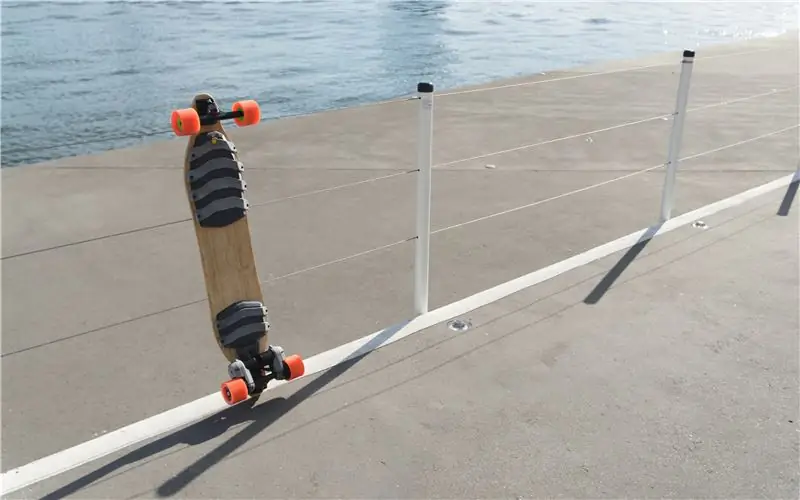
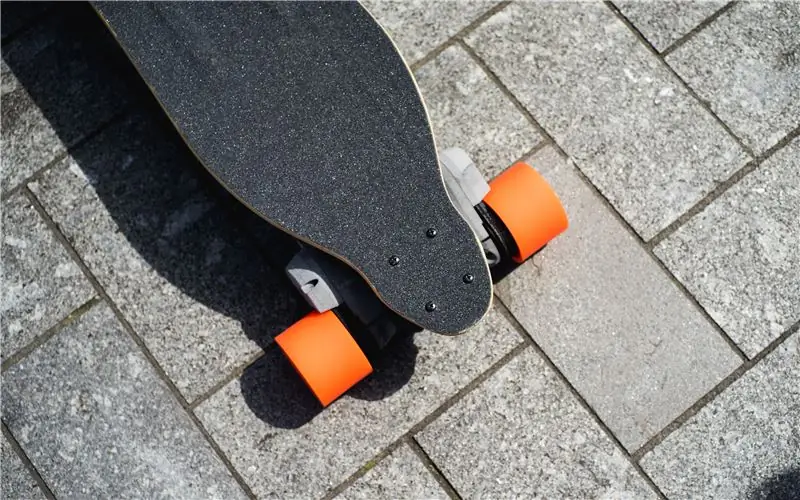
Теперь проект готов! Мы создали отличное видео о доске в действии, вы можете посмотреть его ниже. Большое спасибо 3D Hubs за то, что позволили мне выполнить этот проект - ознакомьтесь с ними здесь, чтобы узнать обо всех своих потребностях в 3D-печати! 3dhubs.com
Рекомендуемые:
Голокрон со светодиодной подсветкой (Звездные войны): сделано в Fusion 360: 18 шагов (с изображениями)
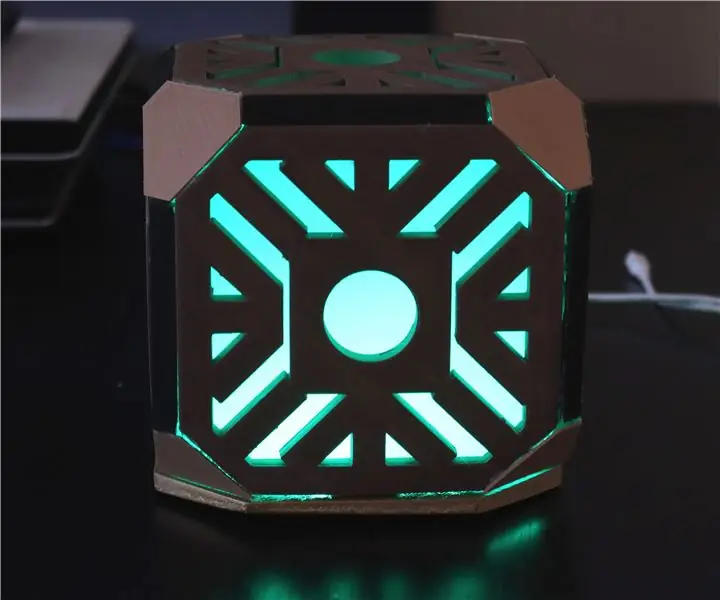
Светодиодный голокрон с подсветкой («Звездные войны»): Сделано в Fusion 360: Мне очень приятно, когда я работаю с Fusion 360 над созданием чего-то красивого, особенно для создания чего-то с освещением. Почему бы не сделать проект, совместив фильм «Звездные войны» с освещением? Поэтому я решил сделать этот поучительный проект
Легкий скейтборд с граффити: 6 шагов (с изображениями)
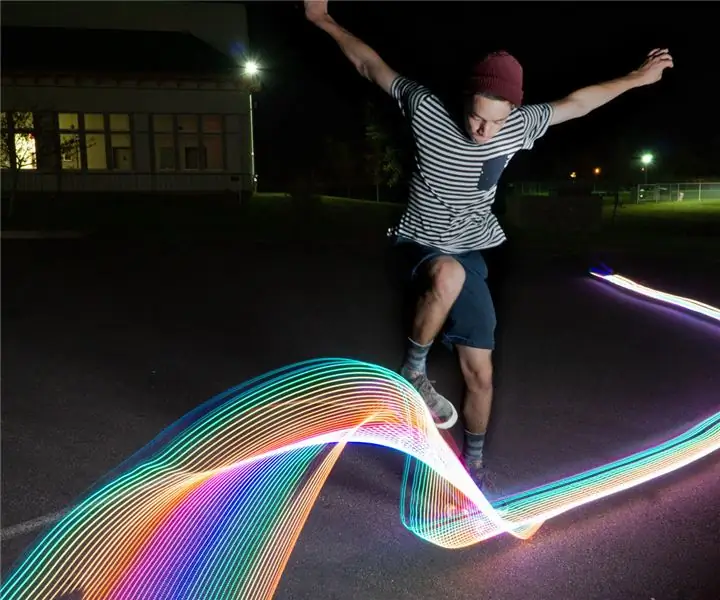
Скейтборд с легким граффити: Раньше я делал легкие граффити, и всегда нахожу результаты и процесс очень интересным. Я хотел сделать еще один шаг и поработать над своим мастерством изготовителя, чтобы построить легкий скейтборд с граффити. Вот как я это сделал
OmniBoard: гибридный скейтборд и ховерборд с управлением по Bluetooth: 19 шагов (с изображениями)
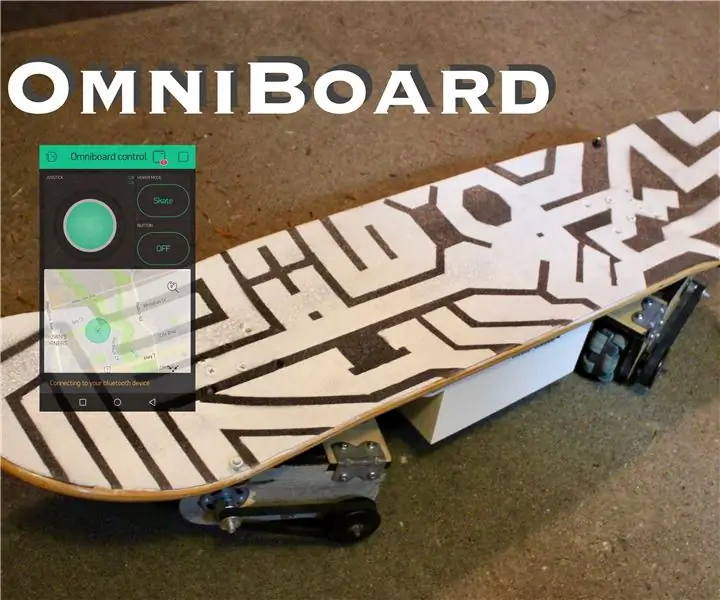
OmniBoard: гибридный скейтборд и ховерборд с управлением по Bluetooth: OmniBoard - это новый гибридный электрический скейтборд-ховерборд, управляемый через приложение для смартфона по Bluetooth. Он может двигаться со всеми тремя степенями свободы, достижимыми обеими досками вместе взятыми, двигаться вперед, вращаться вокруг своей оси и
Скейтборд с микроконтроллером PIC и светодиодами: 8 шагов (с изображениями)
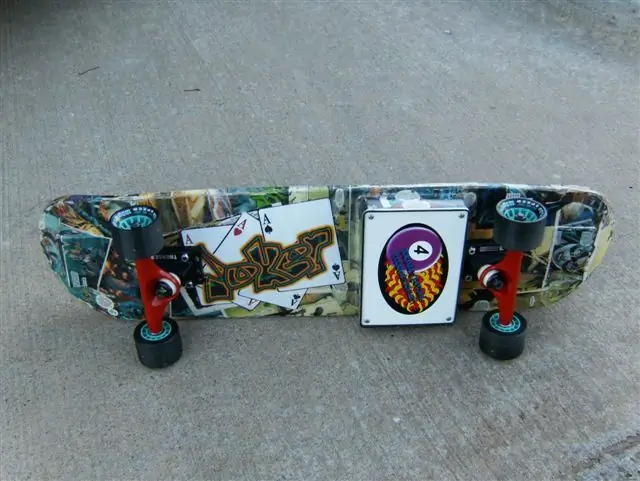
Скейтборд с микроконтроллером PIC и светодиодами: что вы получите, когда инженер-электрик построит скейтборд с нуля для рождественского подарка 13-летнему ребенку? Вы получаете скейтборд с восемью белыми светодиодами (фарами) и восемью красными светодиодами (задние фонари), и все они управляются микрокроллером PIC! И я миг
Сделай сам скейтборд Longboard Riser Lights Угловой Riser: 5 шагов
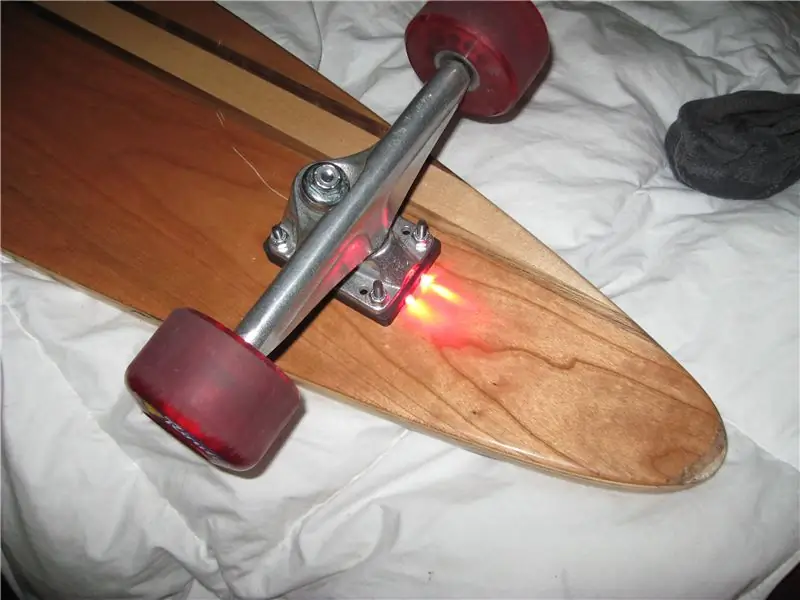
Сделай сам скейтборд Longboard Riser Lights Angled Riser: так что однажды ночью я чуть не попал под машину по дороге к местным волгринам … было очень темно, никаких уличных фонарей, и я понял, что я не очень заметен. Я видел в сети фонари на подступенках … проверил их. слишком дорогой. и мне не нравится тот факт, что