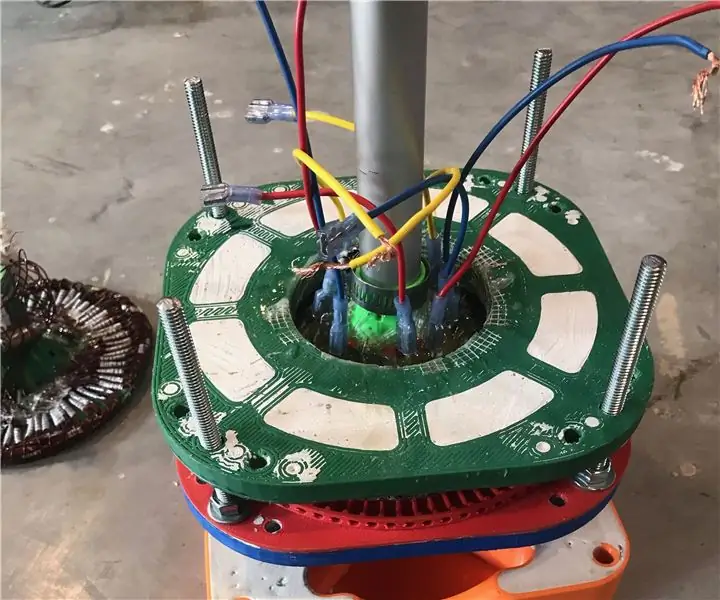
Оглавление:
2025 Автор: John Day | [email protected]. Последнее изменение: 2025-06-01 06:10
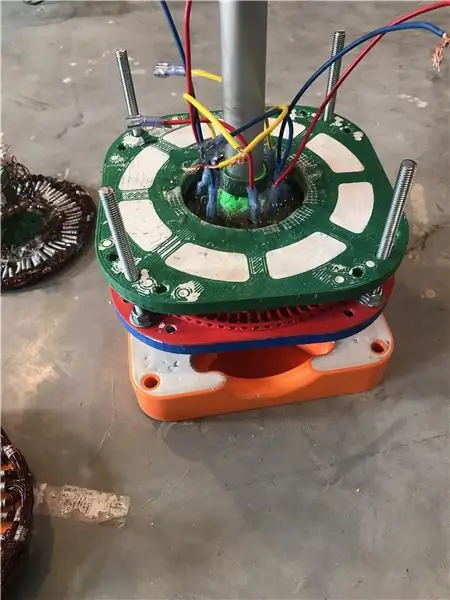
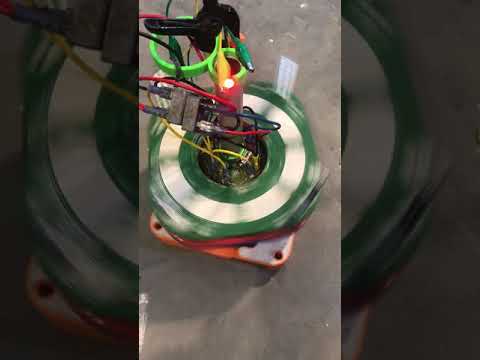
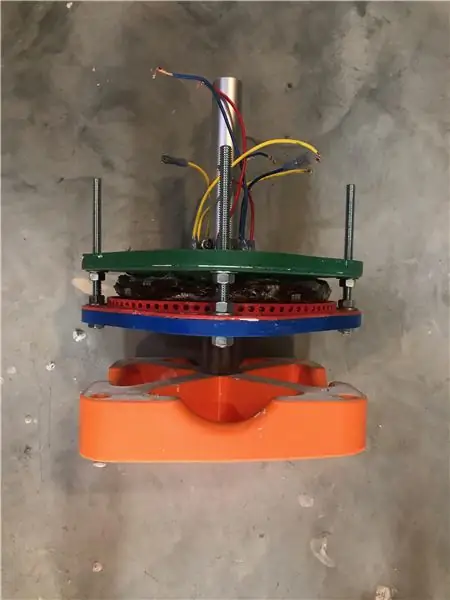
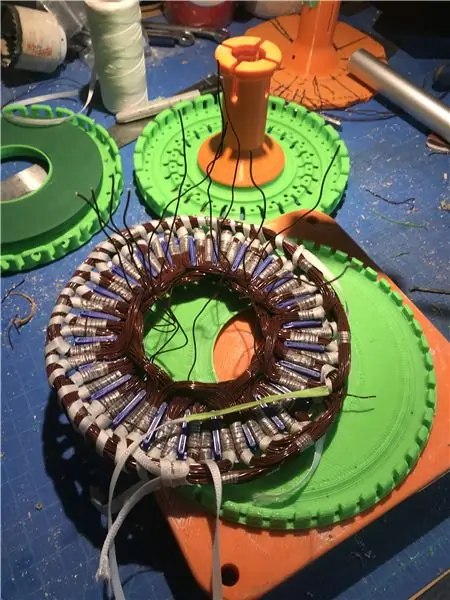
ОСТАНАВЛИВАТЬСЯ!! ПРОЧИТАЙТЕ ЭТО ПЕРВЫЙ !!! Это запись о проекте, который все еще находится в стадии разработки. Пожалуйста, не стесняйтесь предлагать поддержку.
Моя конечная цель - сделать этот тип двигателя / генератора переменного тока параметризованной конструкцией с открытым исходным кодом. Пользователь должен иметь возможность вводить некоторые параметры, такие как крутящий момент, скорость, ток, вольт / об / мин, обычные размеры магнитов и, возможно, доступное пространство, а также необходимо сгенерировать серию файлов для 3D-печати.stl и.dxf.
Я создал платформу, которая может проверить смоделированный дизайн, который затем может быть преобразован сообществом в более оптимальное устройство.
Отчасти это одна из причин, по которой я установил это с помощью динамометра. Динамометр измеряет крутящий момент и скорость, чтобы можно было измерить мощность в л.с. или ватт на валу. В этом случае я построил генератор с проходным неподвижным валом, который упрощает настройку динамометрической системы, и поэтому его можно настроить для работы в качестве двигателя с помощью RC ESC (я надеюсь) и измерения крутящего момента. на выходе, а также скорость, В и А, позволяющие определить КПД двигателя.
Для моих целей он может приводиться в движение двигателем с регулируемой скоростью (избыток от аккумуляторной дрели с понижающей передачей) и измерять входной крутящий момент на валу, а также выходное напряжение и ток, что позволяет добиться реальной эффективности и ожидаемых нагрузок на турбину. для моделирования.
В этом режиме я надеюсь использовать RC ESC, способный к рекуперативному торможению, и, возможно, Arduino для управления нагрузкой, которую несет мой VAWT, для достижения MPPT (Multi Power Point Tracking).
MPPT используется как для управления солнечными, так и для ветряных турбин, но для ветра это немного другое. С ветроэнергетикой большая проблема заключается в том, что, когда скорость ветра удваивается с 10 км / ч до 20 км / ч, энергия, получаемая от ветра, увеличивается кубиком, то есть в 8 раз. Если бы 10 Вт были доступны при 10 км / ч, то 80 Вт доступны при 20 км / ч. Приятно иметь больше энергии, но выходная мощность генераторов только удваивается при удвоении скорости. Так что, если у вас есть идеальный генератор для ветра 20 км / ч, его нагрузка может быть настолько сильной, что при скорости 10 км / ч он даже не запустится.
MPPT использует сверхмощный твердотельный переключатель для очень быстрого отключения, а затем повторного подключения генератора переменного тока. Он позволяет вам регулировать нагрузку на генератор переменного тока, а значение Multi MPPT означает, что вы можете устанавливать разные нагрузки для разных скоростей.
Это очень полезно, поскольку все типы турбин собирают максимальную энергию, когда нагрузка соответствует доступной энергии или скорости ветра.
ТАК
Это не рецепт, хотя я считаю, что его можно скопировать из того, что я опубликовал, и был бы рад предоставить дополнительную информацию, но я предлагаю, что лучшим вариантом было бы предложить мне улучшения до окончания конкурса схем и датчиков., так что я могу рассмотреть, ответить и, возможно, улучшить эту инструкцию.
Я буду продолжать обновлять, исправлять и добавлять информацию, так что, если сейчас это интересно, вы можете захотеть проверить еще раз, но я надеюсь, что немного успею сделать до того, как контест «Сенсоры» закончится 29/19 июля.
Кроме того, я не особо общительный зверь, но время от времени мне нравится похлопывать по спине, и это одна из причин, по которой я здесь:-) Скажите, нравится ли вам смотреть мои работы и вы хотите их увидеть? еще пожалуйста:-)
Этот проект возник потому, что мне нужна была контролируемая нагрузка для тестирования моей конструкции турбины, и я хотел, чтобы она была легко воспроизводимой, чтобы другие тоже могли ее использовать. С этой целью я ограничился разработкой чего-то, что можно было бы построить только с помощью FDM-принтера, без каких-либо других станков. Кажется, что не так много коммерческих продуктов, которые удовлетворяют потребность в генераторах переменного тока с высоким крутящим моментом, низкой скоростью и без зубчатого зацепления, хотя есть несколько из Китая. В целом спрос невелик, потому что зубчатые передачи такие недорогие, а электричество - такое дешевое.
Я хотел что-то, что давало около 12 В при 40-120 об / мин и около 600-750 Вт при 120-200 об / мин. Я также хотел, чтобы он был совместим с недорогими 3-фазными контроллерами PMA из мира RC (электронные контроллеры скорости ESC). Последнее требование заключалось в том, чтобы это был бегунок (корпус или оболочка с магнитами вращается, в то время как вал со статором неподвижен), с валом, который проходит через корпус, и статором, который зажимается на валу.
Работа над этим руководством еще не завершена, и я публикую его для того, чтобы люди могли получить представление о процессе, а не потому, что я считаю, что они должны его скопировать. Ключевую вещь, которую я бы изменил, это то, что проволочная опорная пластина, которую я построил, недостаточно прочна, чтобы должным образом направлять магнитные поля вокруг кольца, поэтому большая часть магнитного потока, заплаченного в этих магнитах, тратится впустую. Когда я переделаю дизайн, что я буду делать в ближайшее время, я, скорее всего, сделаю это с магнитными опорными пластинами в виде стальных пластин, вырезанных на станке с ЧПУ. Сталь была бы довольно недорогой, намного более прочной и упростила бы большую часть этой сборки. Было интересно делать композиты FDM / проволока / гипс, как я проиллюстрировал здесь, и с PLA, загруженным железом, все было бы по-другому. Я решил, что мне нужно что-то действительно долговечное, а именно стальные пластины.
Я добился хороших успехов в этой версии, которую я буду использовать для тестирования этого VAWT. Я еще не совсем подошел к низковольтным характеристикам. Я думаю, что моя мощность / крутящий момент находится на правильном уровне, я буду обновлять по мере развития событий, но на данный момент у меня есть хорошие шансы стать контролируемой нагрузкой, которая мне нужна. Когда он полностью закорочен, кажется, что он способен обеспечить довольно небольшое сопротивление крутящему моменту, более чем достаточное для проверки турбины. Мне просто нужно создать контролируемый банк сопротивления, и у меня есть друг, который помогает мне с этим.
Одна вещь, на которую я кратко остановлюсь, заключается в том, что, как и многие люди сейчас, у меня уже несколько лет есть 3D-принтер (использующий FDM PLA), от которого я получил 20-30 кг удовольствия. Я часто нахожу это разочаровывающим, поскольку детали любого размера / прочности либо дороги и очень медленно печатаются, либо дешевы, быстрые и хрупкие.
Я знаю, сколько тысяч таких 3D-принтеров существует, и они часто ничего не делают, потому что изготовление полезных деталей занимает много времени или слишком дорого. Я придумал интересное решение для более прочных и быстрых деталей из того же принтера и PLA.
Я называю это «литой структурой», где печатный объект (состоящий из 1 или более печатных частей, а иногда и подшипников и валов) состоит из пустот, предназначенных для заполнения затвердевающим жидким наполнителем. Конечно, одним из очевидных вариантов заливки будет что-то вроде эпоксидной смолы, наполненной короткими нитями из рубленого стекловолокна, которую можно использовать для высокопрочных и легких сборок. Я также пробую более дешевые и экологически чистые идеи. Другой стороной этой сборки «литой конструкции» является то, что полость или пустота, которую вы собираетесь заполнить, может иметь элементы малого диаметра, обладающие высокой растяжимостью, натянутые с предварительным натяжением на напечатанную «форму / заглушку», что делает получившуюся структуру композит по материалам и структуре, часть Stressed Skin (оболочка из PLA), но с сердечником с высокой прочностью на сжатие, который также включает элементы с высокой прочностью на растяжение. Я сделаю вторую инструкцию, посвященную этому, поэтому расскажу об этом здесь, только чтобы рассказать, как это относится к этой сборке.
Шаг 1. Список материалов и процесс
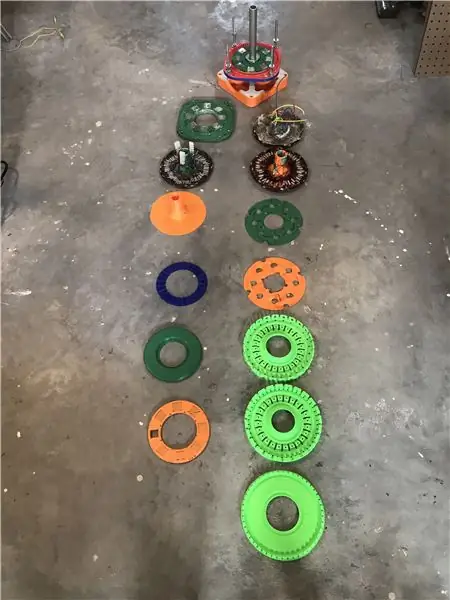
PMA состоит из 3 сборок, каждая из которых содержит или использует различные детали и материалы.
Сверху (со стороны подшипника) вниз (со стороны статора), 1. Подшипниковая опора и верхняя опорная решетка
2. Статор
3. Нижняя магнитная решетка.
1. подшипниковая опора и верхний магнитный массив
Для этого я использовал детали, напечатанные на 3D-принтере, перечисленные выше.
- Верхний магнит 150мм8полюс и опора подшипника CV5.stl,
- внутренняя пластина со стороны подшипника
- внешняя пластина со стороны подшипника
- Самоустанавливающийся подшипник с внутренним диаметром 1 дюйм (например, используемый в стандартных опорных блоках ++, добавьте ссылку в Интернете),
- 25 футов оцинкованной стальной проволоки 24 г
- 15 футов 10 г оцинкованной стальной проволоки
- 2 рулона грубой стальной ваты
По желанию, тяжелая стальная проволока и стальная вата могут быть заменены стальными опорными пластинами, возможна лазерная / водоструйная резка или магнитная опорная пластина, напечатанная на 3D-принтере (но тяжелая стальная проволока по-прежнему является хорошей идеей, поскольку она будет противостоять пластической деформации более время). Я пробовал залить опорную пластину эпоксидной смолой, наполненной порошком оксида железа, и имел некоторый успех. Улучшение магнитной связи между магнитами в решетке сбоку за счет использования более эффективной опорной пластины должно увеличивать выходное напряжение при более низких оборотах в минуту. Также хорошо иметь в виду, что это основной структурный компонент, а задняя пластина передает силы от магнитов к опорным стойкам. Магнитные силы, притягивающие пластины друг к другу, могут составлять сотни фунтов, и силы возрастают экспоненциально (в кубе в третьей степени) по мере приближения пластин друг к другу. Это может быть очень опасно, и следует проявлять осторожность с инструментами и любыми другими предметами, которые могут быть притянуты к собранной пластине или ее задней части!
Я использовал около 300 футов 24-граммового магнитного провода с покрытием в обмотках, о которых я подробно расскажу позже.
Шаг 2: Изготовление магнитных пластин
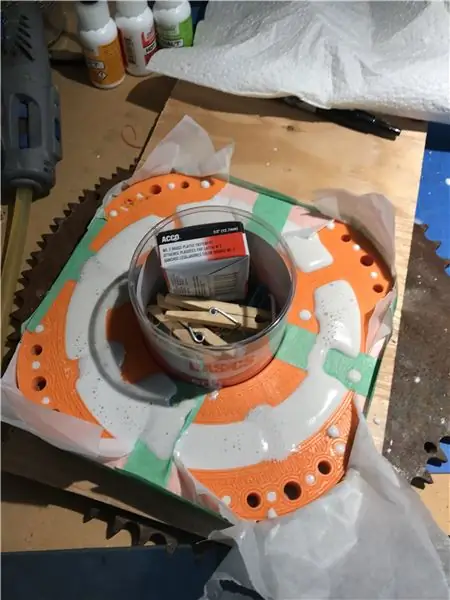
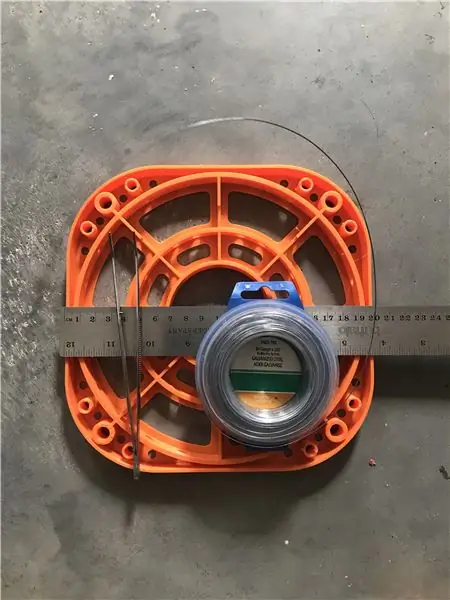
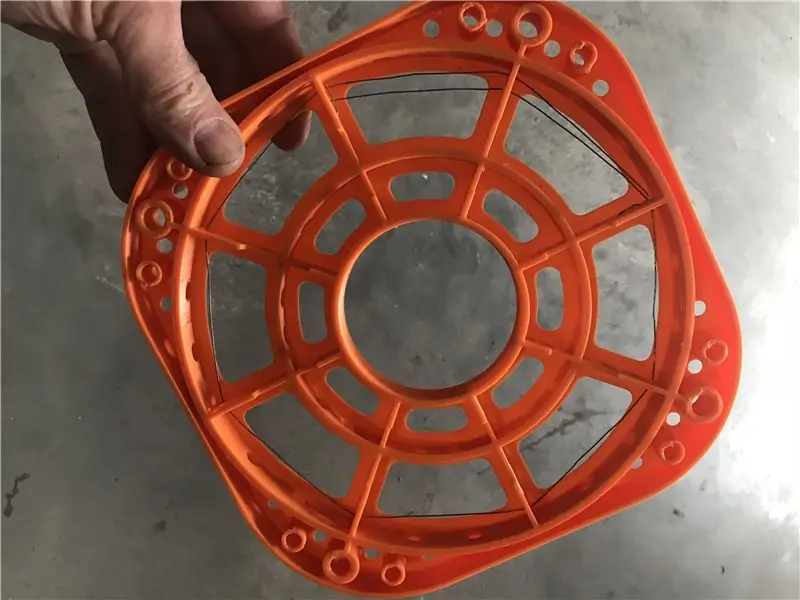
В этом генераторе с осевым магнитным потоком, чтобы минимизировать зубцовые помехи и максимизировать выходную мощность, я использую две группы магнитов, по одной с каждой стороны катушек статора. Это означает, что магнитный сердечник не нужен для прохождения магнитного поля через медные обмотки, как это делают большинство двигателей / альтернативных конфигураций. Есть несколько конструкций с осевым потоком, в которых используются сердечники обозрения, и в будущем я могу попробовать провести несколько экспериментов в этом направлении. Я хотел бы попробовать какой-нибудь материал с железом для 3D-печати.
В данном случае я выбрал 8-полюсный магнитный массив в окружности размером примерно 150 мм, используя редкоземельные магниты 1 x 1 x 0,25 дюйма. Этот размер был необходим для того, чтобы все детали поместились на платформу для печати 210 x 210 мм. В общем, я сначала подбирал этот генератор, понимая, что чем больше диаметр, тем лучше с точки зрения вольт на об / мин, поэтому он сделал его настолько большим, чтобы он удобно поместился на моей печатной платформе. К вашему сведению, есть несколько причин, по которым чем больше, тем лучше: больше места для магниты, чем дальше магниты от центра, тем быстрее они перемещаются, и есть больше места для меди! Все эти вещи могут складываться быстро! Однако я пришел к выводу, что в этом диапазоне размеров обычный Система магнитного потока может быть лучшей домашней сборкой. Маленькие роторы не имеют много места, и все может стать довольно плотным, особенно если вы делаете сквозной вал, как я сделал в этой конструкции. Также, если ваш магнит (радиальная длина) мала по сравнению с диаметром вашего ротора, как в этом (примерно 6 дюймов в диаметре на 1 дюйм магнита), то windi ng становится немного странным, так как обмотка на внутреннем конце составляет всего около 1/2 длины внешнего.
Вернемся к инструктажу! Я собираю магнитные пластины этого генератора переменного тока, сначала приклеивая магнитную пластину (зеленую) к красному фланцу / опорной пластине. Затем я поместил магнитную пластину на несколько тонких слоев фанеры (толщиной около 0,75 дюйма) и поместил оба на толстую стальную пластину, чтобы магниты зажали узел на месте. Затем я намотал стальную проволоку на пластину. позади магнитных пластин. Это пошло не совсем так, как я надеялся. Сильное магнитное поле тянуло провод к центру магнитов, и мне не удалось согнуть каждый ряд провода, чтобы он идеально подходил к следующему месту., не толкая первую обмотку. Я надеялся, что смогу просто намотать провод, и магнитный поток заблокирует его. Затем я попробовал разрезать проволочные кольца, и это было лучше, но все же далеко от того, что я надеялся получить хорошую прочную опорную пластину из проволоки. Возможны более сложные способы сделать это, и, возможно, стоит поэкспериментировать в будущем. Я также пробовал использовать стальную вату, уплотненную в магнитном поле, в качестве опорной пластины или флюса. обратный путь. Похоже, это сработало, но реальная плотность железа оказалась не очень высокой, поэтому я не проверял его эффективность, отчасти потому, что я считал, что проволочная структура важна для механических нагрузок на магнитные пластины. Стальная вата также, возможно, заслуживает дальнейшего изучения, однако следующим вариантом, который я попробую, будут стальные листы, вырезанные гидроабразивной резкой.
Затем я взял оранжевую деталь, напечатанную на 3D-принтере, и протянул проволоку через нее и вокруг нее, как мне показалось, в направлениях максимальной нагрузки, от болта к болту и до центрирования болтов несколько раз на каждом углу. Я также намотал его на отверстия для болтов, где стержень с резьбой проходит как опорные стойки, чтобы сохранить и регулировать расстояние между пластинами.
Убедившись, что магнитная пластина и фланец достаточно хороши, а оранжевая опорная пластина хорошо заправлена арматурной проволокой, я соединил их с помощью клея. Необходимо соблюдать осторожность, так как это клеевое соединение должно быть водонепроницаемым или закрытым. Первые два раза у меня были протечки, и это беспорядок, тратится много штукатурки и больше стресса, чем нужно. Я бы рекомендовал держать под рукой какую-нибудь синюю липкую ленту или другую жевательную резинку, например неперманентный клей, чтобы быстро устранить утечки. После того, как детали будут соединены, заполните их армирующим материалом по вашему выбору. Я использовала твердую штукатурку, модифицированную клеем ПВА. Штукатурка должна достигать 10 000 фунтов на квадратный дюйм при сжатии, но не сильно при растяжении (таким образом, проволока). Я бы хотел попробовать эпоксидную смолу с колотым стеклом и кабосилом, или бетоном с добавками.
В штукатурке удобно то, что после того, как она ударит, у вас будет довольно много времени, когда она будет твердой, но хрупкой, и ее можно легко поцарапать или сбить.
В этой конструкции есть две магнитные пластины. Один из них имеет подшипник, стандартный 1-дюймовый самоустанавливающийся блок опорной подушки. Я сразу вставил свой в магнитную решетку. Для приложения, для которого я его разработал, второй подшипник будет расположен в турбине над генератором переменного тока, поэтому я использовал только один самоустанавливающийся подшипник. В конце концов, это было немного неудобно. Эти детали также можно было бы собрать с каждой магнитной пластиной, имеющей подшипник, если бы выходные провода от статора были пропущены внутрь через установленный вал. позволяют устанавливать пропеллеры противоположного вращения на общий невращающийся вал / трубу.
Шаг 3: Создание статора

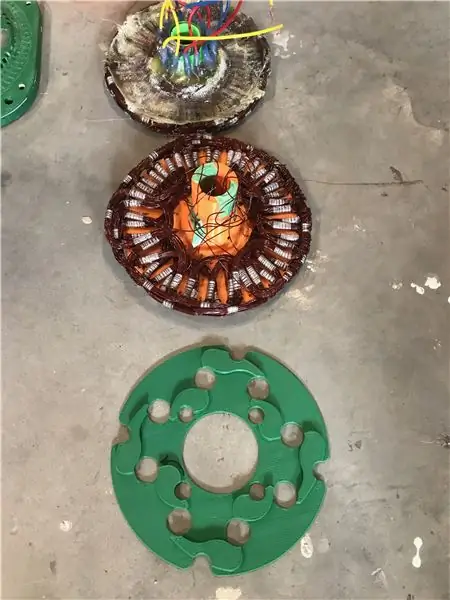
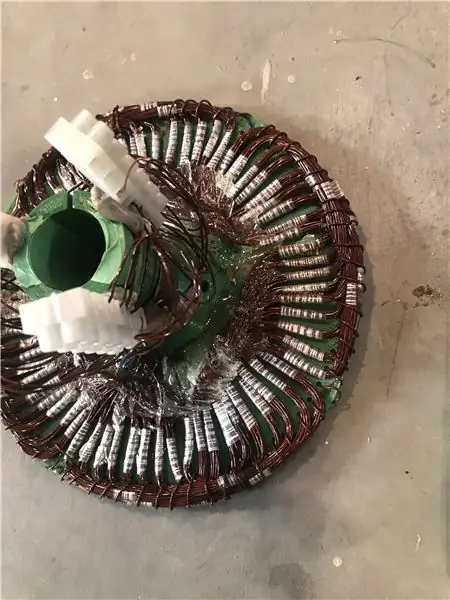
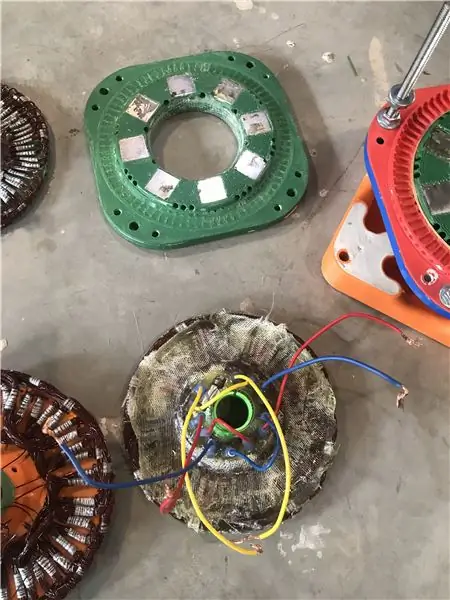
В соответствии с моей целью объяснить, что я сделал и почему в то время это казалось хорошей идеей, для статора потребуется немного больше места.
В ПМА обычно обмотки неподвижны, а магнитные узлы вращаются. Так бывает не всегда, но почти всегда. В узле осевого магнитного потока, с пониманием фундаментального «правила правой руки», понятно, что любой проводник, сталкивающийся с вращающимся магнитным полем, будет иметь ток и напряжение, генерируемые между концами провода, при этом величина полезного тока пропорциональна к направлению поля. Если поле движется параллельно проводу (например, по кругу вокруг оси вращения), полезный ток генерироваться не будет, но будут генерироваться значительные вихревые токи, препятствующие движению магнитов. Если провод проложен перпендикулярно, то будет достигнуто максимальное выходное напряжение и ток.
Другое обобщение состоит в том, что пространство внутри статора, через которое проходит магнитный поток во время вращения, для максимальной выходной мощности должно быть заполнено как можно большим количеством меди, причем все это должно быть уложено радиально, насколько это возможно. Это проблема для систем с осевым потоком малого диаметра, так как в этом случае доступная для меди площадь около вала составляет часть площади на внешнем крае. Можно получить 100% меди в самой внутренней области, с которой сталкивается магнитное поле, но в рамках этой геометрии, которая дает вам, возможно, только 50% на внешнем крае. Это одна из самых веских причин отказаться от слишком малых конструкций осевого потока.
Как я уже сказал ранее, это руководство не о том, как я буду делать это снова, а о том, чтобы указать некоторые направления, которые кажутся многообещающими, и показать некоторые выбоины, которые могут быть достигнуты на этом пути.
При разработке статора я хотел сделать его как можно более гибким с точки зрения выходного напряжения на об / мин, и я хотел, чтобы он был трехфазным. Для максимальной эффективности за счет минимизации генерируемых вихревых токов любая «ножка» (каждая сторона катушки должна рассматриваться как «ножка») должна одновременно контактировать только с одним магнитом. Если магниты расположены близко друг к другу или касаются друг друга, как это имеет место во многих двигателях постоянного тока с высокой выходной мощностью, то в течение времени, когда «ножка» проходит через реверсирование магнитного потока, будут развиваться значительные вихревые токи. В двигателях это не имеет большого значения, поскольку катушка получает питание от контроллера, когда она находится в нужном месте.
Я рассчитал размер магнитного массива с учетом этих концепций. Каждый из восьми магнитов в массиве имеет диаметр 1 дюйм, а расстояние между ними - 1/2 дюйма. Это означает, что магнитный сегмент имеет длину 1,5 дюйма и имеет место для ног 3 x 1/2 дюйма. Каждая «ветвь» - это фаза, поэтому в любой момент одна ветвь видит нейтральный поток, в то время как два других видят восходящий и убывающий потоки. Идеальный трехфазный выход, однако, если дать нейтральной точке такое большое пространство (чтобы минимизировать вихревые токи) и использовать квадратные (или круговые) магниты, поток почти достигает пика на ранней стадии, остается высоким, а затем быстро падает до нуля. Этот тип вывода, я думаю, называется трапециевидным, и может быть трудным для некоторых контроллеров, которые я понимаю. 1-дюймовые круглые магниты в том же аппарате дали бы больше истинной синусоиды.
Как правило, эти домашние генераторы были построены с использованием «катушек», пучков проводов в форме бублика, где каждая сторона бублика представляет собой «ножку», а несколько катушек могут быть соединены вместе, последовательно или параллельно. Пончики расположены по кругу, их центры совмещены с центром пути магнита. Это работает, но есть некоторые проблемы. Одна проблема заключается в том, что, поскольку проводники не радиальные, большая часть проводника не проходит под углом 90 градусов к магнитному полю, поэтому генерируются вихревые токи, которые проявляются в виде тепла в катушке и сопротивления вращению в магнитной матрице.. Другая проблема заключается в том, что поскольку проводники не радиальные, они не так хорошо собираются вместе. Выход прямо пропорционален количеству провода, который вы можете уместить в этом пространстве, поэтому выход снижается из-за нерадиальных «ножек». Хотя это возможно и иногда делается в коммерческих проектах, для намотки катушки с радиальными "ножками", соединенными сверху и снизу, требуется вдвое больше торцевой обмотки, чем для змеевидной обмотки, когда верхняя часть одной ножки соединяется с верхней частью следующая подходящая нога, а затем нижняя часть этой ноги соединяется со следующей соответствующей ногой и так далее.
Другой важный фактор в генераторах с осевым потоком этого типа (вращающиеся магниты над и под статором) - это зазор между пластинами. Это соотношение по закону куба, когда вы уменьшаете расстояние между пластинами на 1/2, плотность магнитного потока увеличивается в 8 раз. Чем тоньше вы сделаете свой статор, тем лучше!
Имея это в виду, я сделал 4-лопастное приспособление для намотки, настроил систему для измерения примерно 50 футов проволочных жил и 6 раз обернул приспособление, создав пучки проволоки диаметром около 6 мм. Я надеваю их на синее дистанционное кольцо, привязывая их через отверстия так, чтобы концы проводов выходили сзади. Это было непросто. Немного помогло то, что я тщательно обмотал жгуты лентой, чтобы они не болтались, а также не торопясь и с помощью гладкого деревянного формовочного инструмента протолкнул провода на место. После того, как все они были связаны на месте, синее промежуточное кольцо было помещено в самую большую из светло-зеленых формующих ванн и с помощью темно-зеленого инструмента для формования пончиков на другой стороне светло-зеленой ванны тщательно прижато к поверхности с помощью скамейки тиски. В этой формовочной ванне есть паз для скручивания проволоки. Это требует времени и терпения, поскольку вы осторожно вращаете примерно на 1/5 оборота, нажимаете, вращаете и продолжаете движение. Это делает диск плоским и тонким, а концевые обмотки могут складываться друг в друга. Вы можете заметить, что у моей 4-лепестковой обмотки прямые «ножки», но внутренние и внешние соединения не круглые. Это должно было облегчить их укладку. Это не сработало. Если бы я делал это снова, я бы сделал так, чтобы внутренние и внешние концевые обмотки следовали по круговой траектории.
После того, как она стала плоской и тонкой, а края сжались, я намотал плоскую ленту вокруг края, чтобы уплотнить ее, а затем еще одну вверх, вниз и вокруг каждой ноги, а затем и на соседнюю. После этого вы можете удалить стяжные проволоки и переключиться на меньшую прижимную ванну, а затем вернуться к тискам и прижать ее как можно тоньше и ровнее. Когда он станет плоским, снимите его с пресс-ванны. Вместо сложного процесса тщательной обработки воском и покрытия форм, подобных этой, антиадгезионными составами, обычно я просто использую пару слоев стрейч-пленки (из кухни). Уложите пару слоев на дно формы и уложите стекловолокно на стретч-пленку. Затем добавьте монтажную трубу статора, которая подходит к верхней части светло-зеленой формовочной ванны, но имеет слой стрейч-пленки и стекловолокна между ними. Затем установите обмотку статора на место, чтобы прижать эластичную пленку и стекловолокно и зафиксировать монтажную трубку статора на месте. Затем вернитесь в тиски и снова прижмите. После того, как он хорошо поместится в ванне, с зажатой эластичной пленкой и стекловолокном, затем добавляется стеклоткань (с отверстием в центре для монтажной трубы статора).
Теперь все готово для заливки связующего материала, обычно используется эпоксидная или полиэфирная смола. Прежде чем это будет сделано, важна тщательная подготовка, поскольку, начав этот процесс, вы уже не сможете остановиться. Я использовал напечатанную на 3D-принтере опорную пластину, которую я ранее сделал, с отверстием диаметром 1 дюйм в центре и плоской пластиной вокруг нее. Я использовал кусок алюминиевой трубки диаметром 1 дюйм размером 16 дюймов, на которую вставлялась трубка для крепления статора. удерживались перпендикулярно плоской пластине. Зеленая формовочная ванна, обмотка статора и монтажная труба статора были сдвинуты вниз, чтобы сесть на плоскую пластину. Перед смешиванием эпоксидной смолы я сначала приготовил 4 куска термоусадочной пленки и осторожно поместил 5-й кусок на пластину. темно-зеленый, формирующий пончик, чтобы у него было минимальное количество морщин на поверхности относительно обмотки статора. После смешивания эпоксидной смолы и заливки ее на стеклоткань я осторожно наложил стрейч-пленку вокруг трубки диаметром 1 дюйм и поместил зеленую образуя кольцо поверх него. Я также приготовил пару старых тормозных роторов, которые придали некоторый вес, и красиво сидел на зеленом формирующем пончике. После этого я поставил перевернутый горшок на тормозные диски, а на него положил около 100 фунтов материала. Я оставил это на 12 часов, и получилось около 4-6 мм толщиной.
Шаг 4: Тестирование и датчики
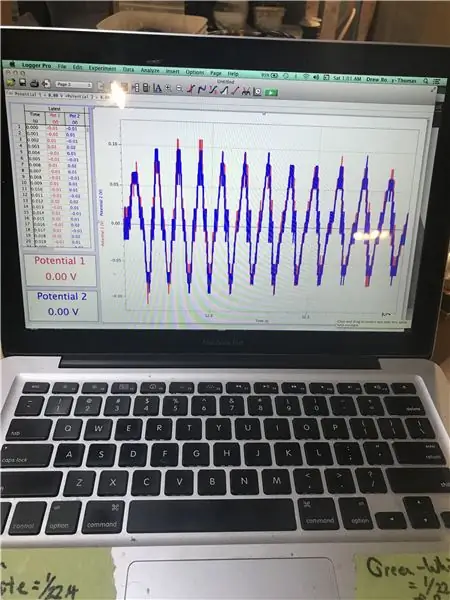
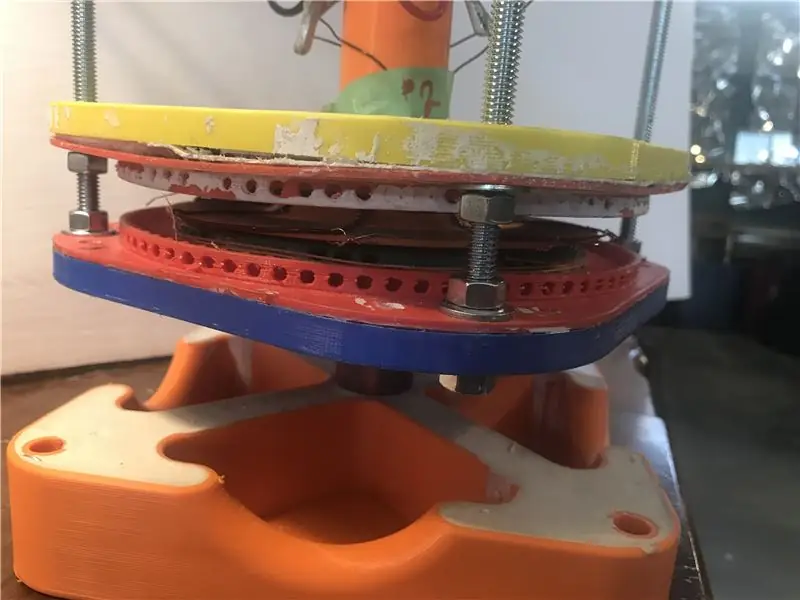
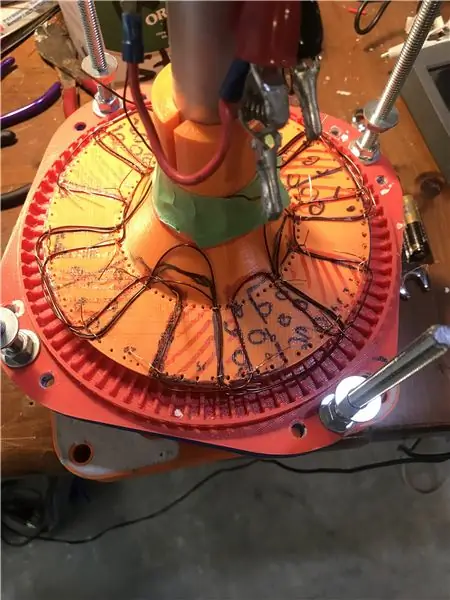
Генератор имеет ряд измеримых входов и выходов, и одновременно измерить их все непросто. Мне очень повезло, что у Vernier есть инструменты, которые значительно упрощают эту задачу. Vernier производит продукты образовательного уровня, не сертифицированные для промышленного использования, но очень полезные для таких экспериментаторов, как я. Я использую логгер данных Vernier с различными датчиками Plug and Play. В этом проекте я использую датчики тока и напряжения Холла для измерения выходной мощности генератора, оптический датчик для определения скорости генератора и датчик нагрузки для измерения входного крутящего момента. Все эти инструменты дискретизируются примерно 1000 раз в секунду и записываются на мой ноутбук с использованием логгера Vernier в качестве устройства сквозной передачи AD. На моем ноутбуке соответствующее программное обеспечение может выполнять вычисления в реальном времени на основе входных данных, комбинируя данные о крутящем моменте и скорости, чтобы получить мощность на входном валу в реальном времени в ваттах и выходные данные в реальном времени в электрических ваттах. Я еще не закончил это тестирование, и мне будет полезно мнение кого-то, кто лучше разбирается в этом.
Проблема, которая возникла у меня, заключается в том, что этот генератор на самом деле является побочным проектом, и поэтому я не хочу тратить на него слишком много времени. Как бы то ни было, я думаю, что могу использовать его в качестве контролируемой нагрузки для моего исследования VAWT, но в конечном итоге я хотел бы работать с людьми, чтобы улучшить его, чтобы он эффективно соответствовал моей турбине.
Когда я начал исследовать VAWT около 15 лет назад, я понял, что тестирование VAWT и других основных факторов является более сложным, чем думает большинство людей.
Основная проблема заключается в том, что энергия, представленная в движущейся жидкости, экспоненциально зависит от скорости ее движения. Это означает, что при удвоении скорости потока энергия, содержащаяся в потоке, увеличивается в 8 раз (она куба). Это проблема, поскольку генераторы более линейны, и, как правило, если вы удвоите частоту вращения генератора в минуту, вы получите примерно в 2 раза большую мощность.
Это фундаментальное несоответствие между турбиной (устройством для сбора энергии) и генератором (мощность на валу и полезная электрическая мощность) затрудняет выбор генератора для ветряной турбины. Если вы выберете генератор переменного тока для своей ветряной турбины, который будет генерировать максимальную мощность, доступную при скорости ветра 20 км / час, он вряд ли даже начнет вращаться до скорости 20-25 км / час, поскольку нагрузка на турбину от генератора переменного тока будет слишком высокой.. При таком согласовании с генератором, когда ветер превышает 20 км, турбина не только улавливает только часть энергии, доступной при ветре с более высокой скоростью, турбина может выйти за пределы скорости и выйти из строя, поскольку нагрузка, обеспечиваемая генератором переменного тока, невысока. достаточно.
В последнее десятилетие решение стало более экономичным из-за падения цен на управляющую электронику. Вместо того, чтобы пытаться согласовать диапазон скоростей, разработчик вычисляет максимальную скорость, на которой устройство должно работать, и выбирает генератор на основе количества энергии и идеальной скорости для турбины на этой скорости или немного выше.. Этот генератор, если он подключен к своей нагрузке, обычно будет обеспечивать слишком большой крутящий момент в диапазоне низких скоростей, и перегруженная турбина не будет улавливать всю энергию, которую она могла бы иметь, если бы была правильно нагружена. Для создания надлежащей нагрузки добавлен контроллер, который на мгновение отключает генератор переменного тока от электрической нагрузки, позволяя турбине набрать нужную скорость, а генератор переменного тока и нагрузка повторно подключаются. Это называется MPPT (отслеживание нескольких точек питания). Контроллер запрограммирован таким образом, что при изменении скорости турбины (или повышении напряжения генератора) генератор переменного тока подключается или отключается примерно тысячу раз в секунду или около того, чтобы соответствовать нагрузке, запрограммированной для этой скорости или напряжения.
Рекомендуемые:
Esp8266 тактовый генератор и генератор импульсов: 3 шага
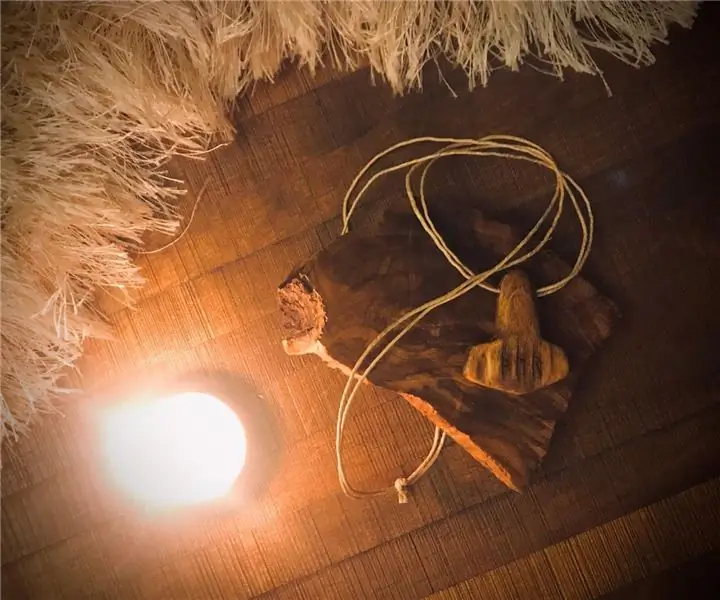
Генератор тактовых импульсов и импульсов Esp8266: Это руководство предназначено для простого тестового оборудования; тактовый генератор и генератор импульсов. Он использует аппаратный интерфейс i2S на esp8266 для генерации тестовых тактовых импульсов или последовательности импульсов. Это упрощает сборку, так как не требуется специального оборудования
Подключение 3-осевого гироскопического датчика BMG160 к Arduino Nano: 5 шагов
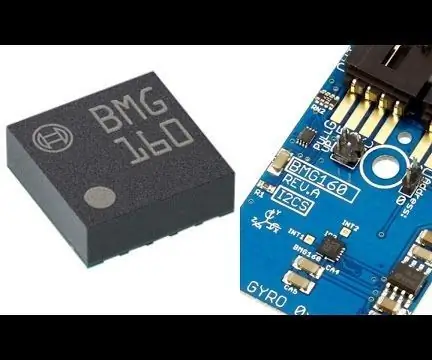
Взаимодействие 3-осевого датчика гироскопа BMG160 с Arduino Nano: в современном мире более половины молодежи и детей увлекаются играми, и все, кто увлекается ими, увлечены техническими аспектами игр, знают важность определения движения в этой сфере. Нас тоже поразило то же самое
Генератор музыки на основе погоды (генератор MIDI на основе ESP8266): 4 шага (с изображениями)
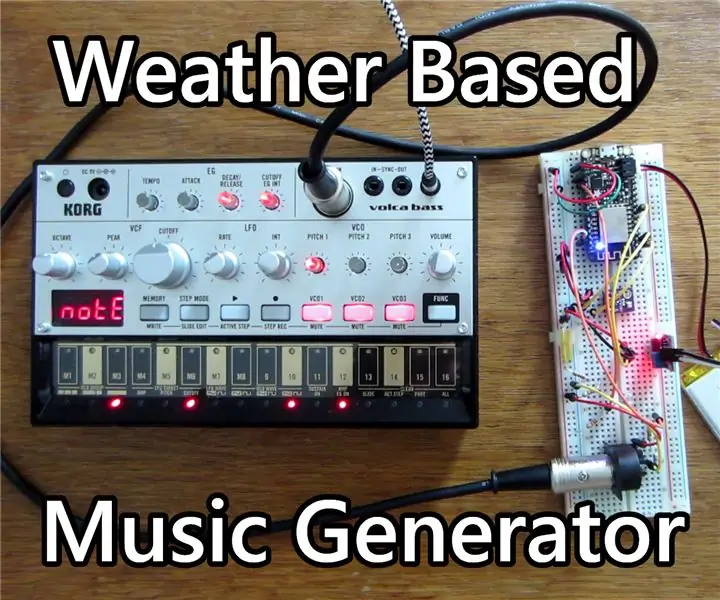
Музыкальный генератор на основе погоды (Midi-генератор на основе ESP8266): Привет, сегодня я объясню, как сделать свой собственный небольшой музыкальный генератор на основе погоды. Он основан на ESP8266, который похож на Arduino, и он реагирует на температуру, дождь. и яркость света. Не ожидайте, что он сделает целые песни или аккордовые программы
Генератор - генератор постоянного тока с использованием геркона: 3 шага
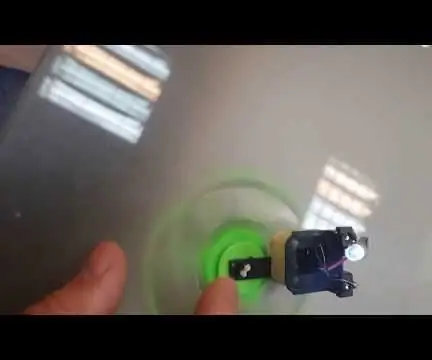
Генератор - генератор постоянного тока, использующий геркон: простой генератор постоянного тока Генератор постоянного тока (DC) - это электрическая машина, которая преобразует механическую энергию в электричество постоянного тока. Важно: генератор постоянного тока (DC) может использоваться в качестве двигателя постоянного тока без какой-либо конструкции. изменения
Измерение скорости потока: 7 шагов (с изображениями)
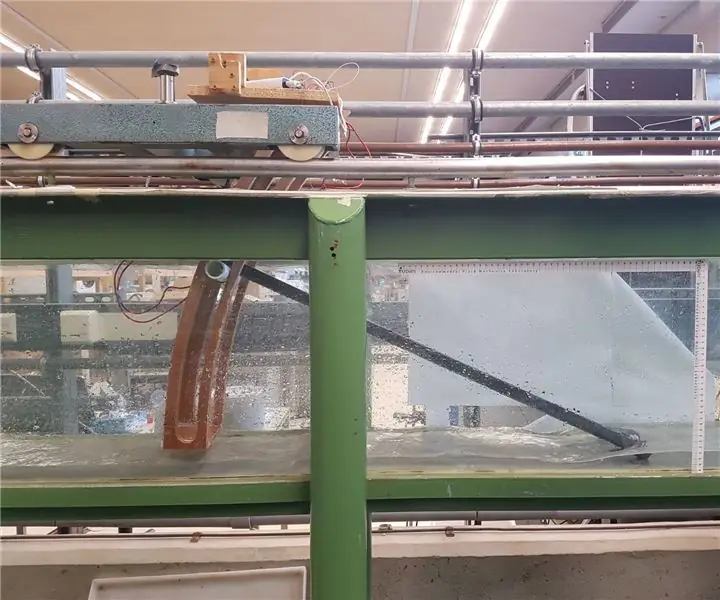
Измерение скорости потока: с помощью этого устройства вы можете измерить скорость свободно текущего потока. Единственное, что необходимо, - это Arduino и некоторые базовые навыки крафтинга и, конечно же, свободный поток. Это не самый практичный способ измерения скорости